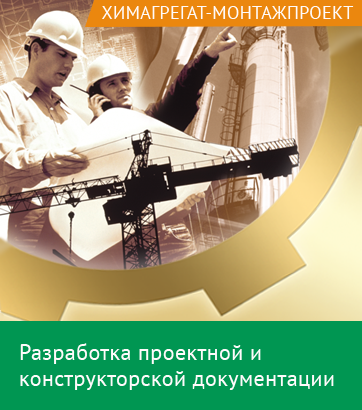
ВОЗМОЖНОСТИ АКУСТИКО-ЭМИССИОННОГО КОНТРОЛЯ
ВОЗМОЖНОСТИ АКУСТИКО-ЭМИССИОННОГО-КОНТРОЛЯ
НА РЕЖИМЕ ДЛЯ ВЫЯВЛЕНИЯ КОРРОЗИОННЫХ ПОВРЕЖДЕНИЙ ТЕХНОЛОГИЧЕСКИХ ТРУБОПРОВОДОВ НЕФТЕХИМИЧЕСКИХ ПРЕДПРИЯТИЙ
А.Н. Мисейко1) – кандидат технических наук, генеральный директор,
В.Г. Харебов1) – лауреат премии Правительства РФ в области науки и техники,
К.А. Медведев1) – заместитель генерального директора по производству,
М.С. Голендухина2) – старший менеджер направления технического надзора и диагностики,
А.В. Чулков2) – главный эксперт направления технического надзора и диагностики,
О.В. Джабраилов2) – главный эксперт направления технического надзора и диагностики
1) ООО «Научно-технический центр «ЭгидА», 2) ПАО «СИБУР Холдинг»
Задача повышения надежности и безопасности нефтехимического оборудования за счет получения достоверной информации о его техническом состоянии в процессе непрерывной эксплуатации и своевременного планирования на её основе технического обслуживания и ремонтов, имеет на сегодняшний день особую актуальность. Это обусловлено с одной стороны потребностью нефтехимических предприятий в современных экономических условиях обеспечивать максимальную фондоотдачу путем увеличения интервалов между капитальными ремонтами оборудования и сокращения времени его простоев, а с другой стороны – необходимостью минимизировать риски возникновения аварий и инцидентов, поскольку в соответствии с реализацией риск-ориентированного подхода в регулировании контрольно-надзорной деятельности существенно возрастает ответственность эксплуатирующих организаций за состояние оборудования. Исходя из этих условий, крайне востребованы эффективные технологии контроля нефтехимического оборудования «на режиме», т.е. без его останова и вывода из эксплуатации.
ООО «Научно-технический центр «ЭгидА» совместно с ООО «ИНТЕРЮНИС-ИТ» разработана технология контроля оборудования «на режиме», основанная на методе акустической эмиссии (АЭ), представляющем собой один из наиболее перспективных методов оценки технического состояния оборудования в режиме реального времени. Метод АЭ позволяет регистрировать с высокой чувствительностью процессы образования и развития дефектов, представляющих опасность для целостности и работоспособности эксплуатируемого оборудования. При разработке технологии акустико-эмиссионного контроля (АЭ-контроля) «на режиме» был использован и обобщен многолетний успешный опыт применения цифровых систем комплексного диагностического мониторинга семейства A-Line/ЛЕЛЬ (изготовитель – ООО «ИНТЕРЮНИС-ИТ»), установленных на статическом оборудовании крупнейших российских нефтехимических и нефтегазоперерабатывающих компаний.
Особенностями разработанной технологии АЭ-контроля оборудования «на режиме» являются:
- использование интеллектуального алгоритма SMART, обеспечивающего с высокой достоверностью обнаружение сигналов АЭ от развивающихся дефектов на фоне различных помех;
- применение специальных волноводных конструкций и смазок, обеспечивающих надежный акустический контакт преобразователей АЭ (ПАЭ) с поверхностью оборудования в широком диапазоне температур;
- использование цифровых помехозащищенных каналов передачи сигналов АЭ;
- применение алгоритма автокалибровки каналов систем A-Line/Лель, нивелирующего риск изменения чувствительности ПАЭ в процессе выполнения контроля «на режиме»;
- использование встроенного набора критериев оценки технического состояния оборудования;
- использование базы данных, содержащей «акустико-эмиссионные портреты» сотен единиц статического оборудования, при определении механизмов действия источников АЭ и степени их опасности.
АЭ-контроль нефтехимического оборудования «на режиме» с использованием данной технологии позволяет сократить время, затрачиваемое на диагностирование оборудования в периоды капитального ремонта, увеличить производительность труда диагностического и ремонтного персонала, снизить вероятность возникновения внеплановых простоев и повысить коэффициент готовности оборудования.
Ключевой особенностью технологии контроля «на режиме», разработанной ООО «Научно-технический центр «ЭгидА» совместно с ООО «ИНТЕРЮНИС-ИТ», является беспороговое обнаружение импульсов АЭ на фоне шумов с помощью уникального алгоритма SMART, основанного на непараметрическом ранговом критерии [1]. В качестве рангового критерия в рамках алгоритма SMART используется двухвыборочная медианная статистика SN:
где RN,i – ранг i-го элемента первой выборки в объединенной выборке, n1 – количество элементов первой выборки, N – количество элементов объединенной выборки. Функция sign равна -1 при отрицательном значении аргумента, 1 при положительном значении аргумента и 0 в случае, если аргумент равен 0.
Критерий SN принимает значения в интервале от –N/2 до N/2 и соответствует доле элементов первой выборки, превышающих медианное значение объединенной выборки. Увеличение значения SN свидетельствует о том, что элементы первой выборки группируются в верхней половине вариационного ряда. Медианный критерий относится к классу простых линейных ранговых статистик и обладает асимптотической нормальностью.
В ранговом алгоритме не используются амплитудные параметры, а обнаружение происходит на основании анализа формы импульсов АЭ, которая характеризуется малым, по сравнению с импульсными составляющими помех, временем нарастания переднего фронта. За счет того, что алгоритм SMART разработан с учетом модели импульса АЭ, он является не чувствительным к импульсным акустическим помехам. Специфичность алгоритма позволяет существенно повысить вероятность обнаружения развивающегося дефекта за счет выявления импульсов АЭ с амплитудой, сопоставимой с уровнем помех.
Исходными данными алгоритма SMART являются цифровые сигналы, зарегистрированные ПАЭ, и преобразованные электронным трактом комплекса A-Line/Лель, включающим усилительный блок, аналоговый и цифровой фильтры, аналого-цифровой преобразователь. Обработка данных АЭ осуществляется независимо по каждому измерительному каналу.
Результат применения алгоритма SMART может быть продемонстрирован на примере выявления импульса АЭ от развивающегося дефекта на фоне постоянно действующей акустической помехи, соответствующей гидродинамическим шумам объекта контроля при турбулентном характере потока рабочей среды [2].
На рисунке 1а показан импульс АЭ на фоне нестационарной помехи, вызванной турбулентным течением жидкости. Импульс АЭ выделен контуром синего цвета, импульсные составляющие помехи – контуром красного цвета. На рисунке 1б показаны значения ранговой статистики SN, рассчитанные для сигнала, приведенного на рисунке 1а. Путём сопоставления значений ранговой статистики возможно достоверное обнаружение импульса АЭ на фоне нестационарной помехи, несмотря на то, что амплитуда импульса АЭ сопоставима с уровнем помех.
а)
б)
Рисунок 1 – Выделение импульса АЭ на фоне помех с помощью алгоритма SMART
а) осциллограмма сигнала, содержащего импульс АЭ и помехи; б) значения ранговой статистики, рассчитанные для сигнала, содержащего импульс АЭ и помехи
В приведенном примере импульс АЭ и импульсные составляющие помехи схожи по форме и близки по амплитуде, несмотря на это импульс АЭ может быть обнаружен с помощью рангового алгоритма за счет большей скорости нарастания переднего фронта. На рисунке 2 показан импульс АЭ (а) и фрагмент помехи (б). Время нарастания, характерное для импульсных составляющих помехи составляет около 1 мс, время нарастания импульса АЭ (при расстоянии 12 м между ПАЭ и источником) – в три раза меньше ~0,3 мс. Различие значений расчётного параметра RA (отношение времени нарастания импульса к его амплитуде) более существенно, поскольку минимальное значение параметра RA для помехи (б) составляет ~300 мc/В, а для импульса АЭ (а) – 75 мс/В. Таким образом, применение беспорогового алгоритма SMART существенно повышает достоверность результатов АЭ-контроля на фоне помех, обусловленных гидродинамическими шумами, вибрацией, кавитацией и т.п.
В реальных производственных условиях алгоритм SMART позволяет выявлять сигналы АЭ от развивающихся дефектов с вероятностью не менее 80% при отношении сигнал/помеха>1,7. Тогда как с помощью стандартной амплитудной дискриминации обнаружение таких сигналов невозможно.
а)
б)
Рисунок 2 – Значения расчётного параметра RA для сигналов различной природы
а) импульс АЭ; б) импульсная составляющая помехи
Безусловным достоинством разработанной технологии АЭ-контроля «на режиме» является возможность её применения для выявления различных типов развивающихся дефектов (трещин, пластической деформации, коррозионно-эрозионных повреждений и т.п.) и оценки технического состояния разнообразного статического нефтехимического оборудования (трубопроводов, сосудов, колонн, реакторов, резервуаров и пр.) непосредственно в процессе эксплуатации. Это достигается за счёт повышения чувствительности метода АЭ при реализации вышеописанного беспорогового алгоритма SMART, минимизации влияния «человеческого фактора» в ходе сбора и обработки АЭ-данных, увеличения точности определения координат источников АЭ. Поскольку разработанная технология позволяет с высокой степенью достоверности идентифицировать даже слабые сигналы АЭ на фоне производственных помех, то для её применения не требуется создавать специальных нагрузок, превышающих значения рабочих параметров, как это обычно принято при проведении АЭ-контроля в условиях стандартных гидро(пневмо)испытаний. Даже малые изменения рабочих параметров в штатном режиме эксплуатации оборудования, могут привести к появлению слабых АЭ-сигналов от развивающихся дефектов, по результатам анализа которых осуществляется оценка технического состояния оборудования.
Весьма важным направлением применения технологии АЭ-контроля нефтехимического оборудования «на режиме» является обнаружение локальных коррозионных повреждений и оценка технического состояния технологических трубопроводов. Проблема коррозии технологических трубопроводов стоит достаточно остро, поскольку по статистике около 70% отказов оборудования нефтехимических и нефтеперерабатывающих предприятий происходит из-за коррозионных повреждений [3].
В качестве одного из примеров успешного применения разработанной технологии для выявления локальных коррозионных повреждений технологических трубопроводов можно привести результаты АЭ-контроля «на режиме» трубопровода подачи углеводородов с верха колонны, на одном из нефтехимических предприятий, входящих в ПАО «СИБУР Холдинг». Данный трубопровод эксплуатируется с 2006 года со следующими параметрами: рабочее давление – 2,1-2,5 МПа, рабочая температура +40оС, рабочая среда (масс. доля компонентов) – метан 4,4%, углеводороды С2 12,7%, углеводороды С3 62,0%, изобутилен 7%, изобутан 3%, окись углерода 0,5%, двуокись углерода 8,9%, азот 1,5%. Трубопровод смонтирован из труб типоразмерами 325×8 мм, 273×8 мм, 219×8 мм, 159×6 мм, 89×5 мм, 57×4 мм, 32×3 мм, 25×3 мм, 18×3,5 мм, которые изготовлены из сталей марок 09Г2С и 20.
Процедура АЭ-контроля «на режиме» вышеописанного трубопровода включала в себя:
- установку ПАЭ на поверхность трубопровода и размотку кабельных линий;
- настройку параметров алгоритма SMART, задание графиков и диаграмм зависимостей различных параметров сигналов АЭ, а также локационных карт для оперативной оценки данных АЭ, регистрируемых в процессе контроля;
- калибровку ПАЭ перед проведением контроля;
- сбор данных АЭ в режиме эксплуатации трубопровода;
- калибровку ПАЭ после проведения контроля;
- демонтаж ПАЭ и смотку кабельных линий;
- обработку и фильтрацию данных АЭ, полученных в результате контроля;
- классификацию и определение степени опасности источников АЭ;
- оценку технического состояния трубопровода в условиях действующих эксплуатационных нагрузок.
АЭ-контроль «на режиме» выполнялся с помощью многоканального цифрового измерительного комплекса A-Line DDM-1, общий вид которого приведен на рисунке 3.
Рисунок 3 – Акустико-эмиссионный цифровой измерительный комплекс A-Line DDM-1
ПАЭ устанавливались на поверхность трубопровода в местах, выбранных на основе информации, полученной при подготовке к контролю. При выборе мест установки ПАЭ учитывалась необходимость надежного контроля зон, в которых наиболее вероятно возникновение и развитие локальных коррозионных повреждений, а также особенности распространения сигналов АЭ, выявленные при проведении измерений затухания и скоростей упругих волн на различных участках трубопровода.
АЭ-контроль «на режиме» трубопровода подачи углеводородов с верха колонны осуществлялся в течение 15 час. 35 мин. на значениях рабочих параметров, соответствующих условиям нормального ведения технологического процесса. Первые 1,5 часа после начала сбора выполнялась предварительная запись и анализ акустического фона объекта контроля с целью определения характеристик шумов, связанных с протеканием технологического процесса и влиянием внешних факторов (погодных условий). По результатам анализа сигналов АЭ, полученных в ходе предварительной записи, были уточнены и скорректированы настроечные параметры алгоритма SMART и продолжен дальнейший сбор данных. В период контроля фиксировались временные тренды изменения основных технологических параметров: давление верха колонны, температура флегмы в колонне, расход флегмы в колонну, расход аб. газа из колонны в отстойник, температура аб. газа в колонну. Также в период выполнения АЭ-контроля «на режиме» трубопровода происходило понижение температуры окружающего воздуха. Тренды изменений рабочих параметров и температуры окружающего воздуха сопоставлялись с временными зависимостями параметров сигналов АЭ и учитывались при последующей обработке данных.
С помощью специальных утилит в составе программного обеспечения комплекса A-Line полученные данные были подвергнуты многоуровневой обработке и фильтрации с целью выделения импульсов АЭ от коррозионных повреждений и исключения шумовых сигналов, обусловленных гидродинамическими и аэродинамическими явлениями при транспортировке рабочей среды по трубопроводу, электромагнитными наводками и синфазными помехами. Специалистами ООО «Научно-технический центр «ЭгидА» было выполнена кластеризация областей на корреляционных диаграммах параметров сигналов АЭ, анализ временных трендов эксплуатационных параметров, обработка осциллограмм и распределений плотности энергии сигналов АЭ от частоты, а также оценка зон повышенной концентрации источников АЭ.
На рисунках 4-7 приведены некоторые зависимости параметров АЭ по каналам комплекса A-Line за время выполнения контроля «на режиме» трубопровода подачи углеводородов с верха колонны, анализ которых позволил установить наличие источников АЭ, соответствующих развивающимся коррозионным повреждениям. Показателями наличия коррозионных повреждений на контролируемых участках трубопровода являлись, в том числе, изменения энергетических параметров, суммы импульсов АЭ, АЭ-активности, числа выбросов сигналов АЭ, скорости счета, соотношений временных параметров импульсов АЭ за период выполнения контроля, а также динамика роста числа лоцируемых источников АЭ при изменениях расхода и температуры рабочей среды. В последнем случае было установлено, что значительная часть источников АЭ, соответствующих развивающимся локальным коррозионным повреждениям, зарегистрирована в моменты изменений расхода аб. газа из колонны в отстойник и температуры аб. газа в колонну, максимальные перепады которых составили 52,5% и 79,6% соответственно. Также часть источников АЭ регистрировалась в моменты времени, совпадающие с изменениями температуры и расхода флегмы в колонну, особенно в последние часы периода контроля «на режиме».
Рисунок 4 – Накопление импульсов АЭ по каждому каналу за время контроля «на режиме»
Рисунок 5 – Изменение АЭ-активности по каждому каналу за время контроля «на режиме»
Рисунок 6 – Изменение выбросов сигналов АЭ по каждому каналу за время контроля «на режиме»
Рисунок 7 – Изменение скорости счёта АЭ по каждому каналу за время контроля «на режиме»
Всего на контролируемых участках трубопровода подачи углеводородов с верха колонны было выявлено 8 зон источников АЭ, из которых согласно классификации по ГОСТ Р 52727-2007: 1 зона пассивных источников (1 класс), 2 зоны активных источников (2 класс) и 5 зон критически активных источников (3 класс). Катастрофически активных источников (4 класс) по ГОСТ Р 52727-2007 зарегистрировано не было. Соответственно, наибольшую значимость для оценки технического состояния трубопровода имели дефекты, расположенные в зонах критически активных источников АЭ. Из них особое внимание было уделено трём зонам, места расположения которых совпадали с врезками, отводами и тупиковыми участками трубопровода, являющимися факторами, существенно повышающими риск ускоренной коррозии. Зона №1 была зарегистрирована на участке выходного коллектора АВЗ от заглушки 273×8 мм до врезки трубы 219×8 мм (начало зоны в месте установки ПАЭ1, конец зоны – 300 мм от места установки ПАЭ1 в сторону ПАЭ2), зона №2 также располагалась на данном коллекторе между ПАЭ4 и ПАЭ5 (протяженность зоны 1200 мм), зона №3 охватывала две «катушки» и один отвод 900-159×6 мм на участке поблизости от входа в колонну (начало зоны в месте установки ПАЭ14, конец зоны – 1050 мм от места установки ПАЭ14 в сторону ПАЭ15). Координаты зон №№1-3 на локационных картах и общий вид соответствующих им элементов трубопровода приведены на рисунках 8 и 9.
Все зоны критически активных источников АЭ были подвергнуты наружному осмотру и ультразвуковой толщинометрии. Наружная поверхность трубопровода в местах регистрации зон №№1, 2 имела равномерный коррозионный износ, без явно выраженных повреждений. Однако, по результатам ультразвуковой толщинометрии коллектора в зонах №№1, 2 были выявлены локальные утонения до 40% от номинальной толщины стенки, что свидетельствует о наличии интенсивной язвенной коррозии на внутренней поверхности трубопровода. В зоне №3 при наружном осмотре были обнаружены многочисленные коррозионные язвы диаметром до 7 мм и глубиной до 0,5 мм на поверхности отвода 900-159×6 мм и примыкающих к нему «катушек», при этом ультразвуковая толщинометрия в указанной зоне позволила установить также наличие значительного коррозионного износа на внутренней поверхности – до 55% от номинальной толщины стенки (измеренная толщина – 2,7 мм, номинальная толщина – 6,0 мм).
а)
б)
в)
Рисунок 8 – Общий вид трубопровода в зонах №№1, 2 и координаты локации зон
а) общий вид элементов коллектора АВЗ в местах регистрации зон №№1, 2;
б) локационная карта участка ПАЭ1-ПАЭ2; в) локационная карта участка ПАЭ4-ПАЭ5
а)
б)
в)
Рисунок 9 – Общий вид трубопровода в зоне №3 и координаты локации зоны
а) общий вид элементов трубопровода в зоне №3; б) коррозионные язвы на поверхности отвода в зоне №3; в) локационная карта участка ПАЭ14-ПАЭ15
В соответствии с разработанной технологией АЭ-контроля «на режиме» оценка технического состояния нефтехимического оборудования выполняется на основании наличия зон источников АЭ соответствующих классов по ГОСТ Р 52727-2007 и предусматривает следующую градацию: удовлетворительное состояние (эксплуатация оборудования может осуществляться без дополнительных мероприятий и снижения рабочих параметров); состояние, требующее внимания (в местах регистрации источников АЭ требуется дополнительный контроль, при необходимости – разработка компенсирующих мероприятий и/или снижение рабочих параметров); критическое состояние (требуется дополнительный контроль и при необходимости – ремонт/замена элементов оборудования в местах регистрации источников АЭ); предельное состояние (необходим останов оборудования и его полная замена).
Согласно вышеописанной градации техническое состояние трубопровода подачи углеводородов с верха колонны по результатам АЭ-контроля «на режиме» было оценено как критическое. В местах регистрации зон критически активных и активных источников АЭ было рекомендовано осуществлять дополнительный периодический контроль неразрушающими методами и провести ремонт/замену изношенных элементов в период капитального ремонта. Также было рекомендовано в следующий останов трубопровода выполнить выборочный видеоэндоскопический контроль внутренней поверхности трубопровода в местах разборных соединений.
Таким образом, приведенный пример демонстрирует большие возможности технологии АЭ-контроля «на режиме», разработанной ООО «НТЦ «ЭгидА» и ООО «ИНТЕРЮНИС-ИТ», для выявления коррозионных повреждений технологических трубопроводов нефтехимических предприятий и обеспечения их надежной и безопасной эксплуатации в межремонтный пробег.
БИБЛИОГРАФИЧЕСКИЙ СПИСОК
1. Пат. 2660403 Российская Федерация, МПК G01N 29/14. Способ беспороговой автоматической интеллектуальной регистрации сигналов акустической эмиссии устройством неразрушающего контроля / Барат В.А., Шиманский А.Г.; заявитель и патентообладатель ООО «ИНТЕРЮНИС-ИТ». – №2017103185, заявл. 01.02.2017; опубл. 06.07.2018, Бюл. № 19.
2. Елизаров С.В., Барат В.А., Шиманский А.Г. Интеллектуальная акустико-эмиссионная система SMART нового поколения // В мире НК. – 2016, №3(65), с. 26-29.
3. Бурлов В.В., Алцыбеева А.И., Кузинова Т.М. Система защиты от коррозии оборудования переработки нефти. – СПб.: ЦОП «Профессия», 2015. – 336 с.
