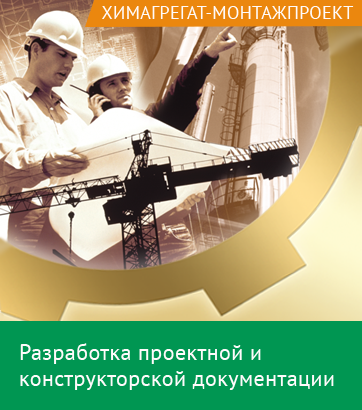
УСТАНОВКА КОМПРИМИРОВАНИЯ ДИОКСИДА УГЛЕРОДА
С. В. Афанасьев, к.х.н., д.т.н., доцент по специальности «Экология»,
начальник Управления по разработке инноваций и патентованию АО «ТОАЗ»
Углекислый газ является наиболее крупнотоннажным среди других парниковых газов, и именно ему отведена ведущая роль в потеплении климата на нашей планете [1]. Основными источниками его попадания в атмосферу являются дымовые газы с предприятий теплоэнергетики, нефте- и газохимии, металлургия, а также выбросы автотранспорта [2;3]. В соответствии с Парижским соглашением по климату в достаточно сложном положении в ближайшие годы могут оказаться и многие промышленные предприятия по выпуску аммиака и карбамида. По указанной причине на первый план сегодня выходят задачи по снижению удельных энергозатрат и расходных коэффициентов по природному газу. Их решение напрямую зависит от внедрения новых энергосберегающих технологических процессов, а также от включения в технологическую схему стадии компримирования углекислого газа с использованием холодильных машин усовершенствованной конструкции.
К этому важно добавить, что образующийся в крупнотоннажном производстве аммиака диоксид углерода лишь частично используется в различных отраслях промышленности. По указанной причине наиболее важными являются производства карбамида, метанола и ряда других продуктов.
К числу перспективных могут быть отнесены и предприятия, занятые добычей высоковязких нефтей [4]. Это связано с тем, что залегающая в пластах нефть при контакте с диоксидом углерода снижает свою вязкость, что облегчает процесс нефтедобычи. Данный метод относится к числу наиболее высокопотенциальных, способный снижать до 2–5 % остаточную нефтенасыщенность призабойной зоны. Применительно к российским нефтедобывающим организациям указанный инновационный приём имеет принципиальное значение, так как основная часть остаточной нефти на известных разрабатываемых месторождениях остается в виде заводненных запасов, которые труднее извлекать, чем из обычных пластов. По имеющимся данным, СО2 диффундирует в нефть значительно лучше метана и его газообразных гомологов, при этом растворимость увеличивается с ростом давления и молекулярной массы нефти. Контактируя с нефтью, углекислый газ частично распределяется в ней, и одновременно экстрагирует углеводороды, обогащаясь ими. В результате давление, необходимое для вытеснения нефти диоксидом углерода, в 3 раза меньше, чем одним углеводородным газом.
Быстро развивающимся направлением промышленного использования углекислого газа ныне является синтез карбамида. Для увеличения выхода азотного удобрения предлагаются решения, основанные на производстве жидкого низкотемпературного диоксида углерода. Их существенным недостатком являются высокие энергетические затраты на выпуск товарной продукции, что в значительной степени обусловлено необходимостью компримирования СО2 перед его подачей в реактор синтеза. На основе опыта эксплуатации углекислотных установок были выявлены узкие места, мешающие наращиванию объемов производства, а также их высокие энергозатраты из-за несовершенства технологических схем [5; 6]. Признано целесообразным использование компрессорно-насосной углекислотной установки, в которой эффективно сочетается процесс получения жидкого диоксида углерода при пониженном давлении, и подачи компримированного газа с необходимым давлением (15 МПа) с помощью низкотемпературного насоса в агрегат синтеза карбамида.
В отличие от традиционной технологии подготовка газообразного СО2 для дальнейшего использования в производстве карбамида проводится в два этапа: вначале давление повышается с 0,1 МПа до 3,0 МПа, после чего проводится его охлаждение с использованием холода газификации компримированного до 15 МПа жидкого диоксида углерода. Для конденсации газообразного углекислого газа может быть применена абсорбционная водоаммиачная холодильная машина, использующая для производства холода теплоту компримирования СО2 в центробежном компрессоре [7]. Благодаря модернизации турбокомпрессорного агрегата можно добиться существенного увеличения выхода конечного продукта.
Целью проведенного нами исследования являлось дальнейшее повышение энергосбережения технологической стадии получения диоксида углерода высокого давления путем комбинированного использования компрессорного и насосного оборудования.
Поставленная задача была решена с помощью установки компримирования диоксида углерода, включающей углекислотный компрессор, блок осушки, рекуперативный теплообменник, бромистолитиевую холодильную машину и сепаратор накопления низкотемпературного жидкого диоксида углерода, причем перевод компримированного газообразного диоксида углерода в жидкое состояние достигается за счет съема тепла в рекуперативном теплообменнике и использования холода жидкого аммиака в конденсаторе СО2 , с дальнейшим отделением несконденсированных газов в сепараторе, а сжатие сжиженного диоксида углерода осуществляется в плунжерном низкотемпературном насосе до давления 15 МПа, с его газификацией в рекуперативном теплообменнике [8].
Принципиальная схема предлагаемой установки ожижения диоксида углерода приведена на рисунке.
Газообразный диоксид углерода сжимается в компрессоре 11 до давления 1,7 МПа, проходит блок осушки 10 и охлаждается в рекуперативном теплообменнике 9. В конденсаторе 6 он переходит в жидкое состояние за счёт холода жидкого аммиака, поступающего в конденсатор аммиака 4. Сжиженный диоксид углерода направляется в сепаратор 7 для отделения несконденсированных газов, которые подаются на регенерацию и охлаждение блока осушки 11, а затем сбрасываются в атмосферу. Жидкий СО2, отводимый из сепаратора 7, сжимается в низкотемпературном плунжерном насосе 8 до давления 15 МПа, затем газифицируется в рекуперативном теплообменнике 9 за счёт подвода тепла от компримированного в компрессоре 1 газообразного СО2 и далее подаётся на производство карбамида.
Переохлаждённый сжиженный аммиак с температурой -34оС при давлении 1,7 МПа, нагревается в конденсаторе диоксида углерода 6 до температуры минус 15оС и поступает в конденсатор аммиака 4. В свою очередь, тёплый аммиак (рециркулирующий поток) с температурой +40оС при давлении 1,7 МПа переохлаждается до +15 0 С в водяном теплообменнике 1 абсорбционной бромистолитиевой машины 2, после чего направляется в ресивер жидкого аммиака 5. Абсорбционная бромистолитиевая холодильная машина, потребляя водяной пар низкого потенциала с давлением 0,35-0,6 МПа вырабатывает холодную воду с температурой 5 – 7 оС, которой и охлаждает теплообменник 1.
В ресивере 5 происходит смешение рециркулирующего потока жидкого аммиака со свежей порцией холодного аммиака, который нагревается в конденсаторе паров аммиака 4 до температуры +30оС. При этом несконденсированные примеси (инерты) отводятся на свечу после предварительной очистки их от остаточных паров аммиака (на схеме не показано).
Из ресивера 5 жидкий аммиак при температуре +30оС и давлении 1,7 МПа подаётся на сжатие в плунжерный аммиачный насос высокого давления 3, который сжимает его до 15 МПа и подаёт на синтез карбамида.
Предлагаемая схема производства жидкого диоксида углерода (за счёт холода низкотемпературного потока жидкого NH3) и подачи его насосом на синтез карбамида обладает следующими преимуществами:
Во-первых, газообразный диоксид углерода сжимается в компрессоре только до 1,7 МПа, а не до более высоких давлений, как в традиционной схеме. Во-вторых, конденсация СО2 осуществляется за счёт полезного использования холода переохлаждённого жидкого аммиака, подаваемого на производство карбамида, т.е. без энергозатрат на производство холода. В-третьих, после конденсации углекислого газа из сепаратора удаляются в атмосферу неконденсирующиеся газы (инерты). Это способствует получению чистого СО2 без примесей. В-четвёртых, дальнейшее сжатие жидкого диоксида углерода может быть доведено в насосе до оптимального давления синтеза карбамида. При этом важно отметить, что работа сжатия насоса более, чем на порядок, ниже работы сжатия компрессора от 1,7 МПа до 15 МПа. В-пятых, снижается на 50% расход воды на охлаждение углекислотного компрессора.
Указанная компрессорно-насосная установка, действующая в составе агрегатов синтеза аммиака и карбамида, позволяет при нагреве холодного аммиака от -30оС до -15оС при давлении 1,7 МПа в количестве 41 т/ч произвести 11 т/ч жидкого диоксида углерода с давлением 15 МПа, что соответствует объёмному расходу 6000 нм3/ч. Удельный расход электроэнергии на ожижение и компримирование СО2 до давления 15,0 МПа составляет 0,1 кВт·ч/кг, что на 25 % ниже затрат энергии показателя установок, описанных в литературе.
Список литературы.
1.Афанасьев С.В., Шевченко Ю.Н., Сергеев С.П. Новые технические решения для получения диоксида углерода // Вектор науки ТГУ. 2017. №2(40). С. 11 – 16.
2.Афанасьев С.В. Установка переработки дымовых газов с получением диоксида углерода как способ снижения «углеродного следа». Химагрегаты. Специализированный журнал по химоборудованию. 2022. №3 (59). С.32 – 34.
3.Патент RU№ 2733774. Способ выделения диоксида углерода из дымовых газов и устройство для осуществления способа. МПК В01D 53/62; B01D 53/00// Заявка № 2020106740, Опубл. 06.10.2020 г. Бюл. № 28
4.Афанасьев С.В. Углекислый газ как сырьё для крупнотоннажной химии// Neftegaz.ru. Деловой журнал. 2019. №9. С.94 – 106.
5.Афанасьев С.В., Сергеев С.П., Волков В.А. Современные направления производства и переработки диоксида углерода // Химическая техника. 2016. № 11. С. 30–33.
6.Афанасьев С.В., Капитонов М.С., Лисовская Л.В. Совершенствование технологии и оборудования крупнотоннажного производства диоксида углерода // Технические газы. 2007. № 3. С. 51–55.
7.Лавренченко Г.К., Копытов А.В., Афанасьев С.В., Рощенко О.С. Повышение эффективности подачи диоксида углерода на синтез карбамида // Технические газы. 2011. № 2. С. 27–31.
8.Патент на полезную модель RU№90544. Установка компримирования диоксида углерода. МПК F25J 1/00// Заявка №200911617/22. Опубл. 10.01.2010. Бюл. №1.
