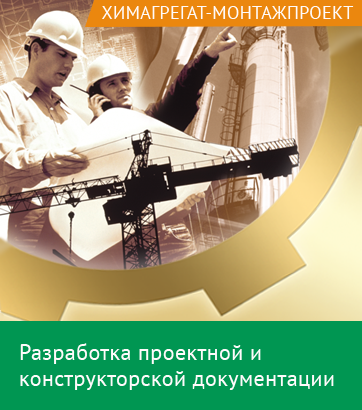
РЕАКТОР КАТАЛИТИЧЕСКОГО ОКИСЛЕНИЯ МЕТАНОЛА В ФОРМАЛЬДЕГИД
С.В. Афанасьев, ПАО «ТОАЗ», г. Тольятти, Россия
Производство формальдегида относится к многотоннажным благодаря его широкому применению в нефтедобыче в качестве компонента нейтрализатора сероводорода, а также для производства широкого ассортимента карбамидоформальдегидных смол, пластмасс, синтетических волокон, взрывчатых веществ, лекарственных препаратов. В настоящее время его синтезируют преимущественно окислением метанола на железо-молибденовых катализаторах при температуре 250-400 °С. Процесс осуществляется в аппаратах специальной конструкции, наиболее распространенным типом которых являются трубчатые реакторы.
Конструкция подобных аппаратов и принцип их действия подробно рассмотрены в работах [1 - 3]. Их устройство предусматривает заполнение стальных трубок диаметром 15-25 мм и длиной 800 – 1400 мм железо-молибденовым катализатором и возможность подачи в межтрубное пространство теплоносителя, охлаждающего катализатор и продукты реакции. Процесс в реакторах подобного типа выполняется с внутренним теплоотводом в условиях, близких к изотермическим.
В связи с тем, что максимум температуры находится в средней части контактного аппарата и здесь же расположена область максимальной параметрической чувствительности, ввод теплоносителя производится в центральную часть межтрубного пространства, а вывод осуществляется снизу и сверху.
Несовершенством данной конструкции является высокое содержание метанола в формальдегид-содержащем газе, для снижения которого до требуемого уровня необходимо использовать встроенную в реактор адиабатическую приставку, заполненную слоем катализатора.
Отмеченные недостатки были устранены авторами [4;5]. Это достигнуто совершенствованием конструкции каталитического реактора. Реализованные на площадке ПАО «ТОАЗ» аппараты окислительного дегидрирования метанола в формальдегид содержат встроенный трубный пучок с внутренним диаметром трубок 16 – 25 мм и длиной 900 – 1500 мм, заполненных железо-молибденовым катализатором и керамической инертной насадкой в соотношении 3,5-5 : 1 по объему, разделенных на 4 зоны с 12 секторами в каждой, причем во все зоны радиально по периферии трубного пучка с равномерным смещением относительно друг друга подается теплоноситель для съема тепла, а его вывод осуществляется по центру и верхнюю часть аппарата.
На рис. 1 «а», «б» и «в» показан общий вид реализованной инновационной конструкции.
Рис. 1а
Рис. 1 б
Рис. 1 в
Рисунок 1. 1 - предохранительная мембрана; 2,3 – штуцеры ввода теплоносителя; 4 – смотровое окно; 5 - опора
Реактор окислительного дегидрирования метанола для промышленного производства формальдегид-содержащего газа представляет собой стальной теплоизолированный аппарат диаметром 4000 мм, в котором в трубных досках установлены 10800 трубок длиной 1100 мм с диаметром 25х2 мм, имеющих суммарную площадь теплообмена 803 м2 (Рис.1 «а»). Трубная доска разделена равномерно на 12 секторов, в каждом из которых находится по 900 отверстий определённого размера (Рис.1 «б»). Вставленные в них трубки на 75 % длины заполнены железо-молибденовым катализатором марки КН-26С, состоящим из 80 % мас. МоО3 и 20 % мас. Fe2O3, а верхняя часть – инертной керамической насадкой. В секторах имеются 8 незаполненных трубок, предназначенных для установки термопар. Реактор снабжен штуцерами (симметрично по два в каждую из 4 зон) для входа теплоносителя и двенадцатью для вывода в центральную часть.
Для защиты реактора от разрушения при взрыве газовой смеси на верхней крышке установлены четыре предохранительных мембраны с давлением срабатывания 0,41 – 0,51 МПа (Рис.1«в»).
Теплоноситель (диатермическое масло АМТ-300 У) подается в межтрубное пространство четырех зон реактора радиально по периферии трубного пучка, расположенных одна над другой [5]. Поступление в них масла осуществляется насосами и регулируется клапанами. Установленная по периметру реактора сетка обечайка с отверстиями 4,3 мм обеспечивает равномерную подачу масла в каждый сектор. Конструкция реактора предусматривает установку термопар, контролирующих температуру теплоносителя и катализатора во всем объеме аппарата.
Его работа осуществляется следующим образом.
В верхнюю часть контактного аппарата подается подогретая до 190 – 2100С спирто-воздушная смесь, содержащая 6 – 8 % об. метанола и 8 – 11 % об. кислорода. При температуре 220 – 240 0С (условие зажигания катализатора) в верхней зоне трубного пучка начинается процесс образования формальдегида, сопровождающийся большим выделением тепла. По мере перемещения спирто-воздушной смеси к середине трубок происходит рост температуры с одновременным повышением конверсии метанола. Съем тепла осуществляется подачей масла АМТ-30У во все четыре зоны реактора. Проходя через межтрубное пространство к центру аппарата теплоноситель забирает тепло реакции от трубок и поступает в котел-утилизатор, где тепло расходуется на производство пара. Состав газовой смеси на выходе из реактора определяется профилем температуры по высоте аппарата, который в свою очередь зависит от содержания метанола и кислорода в спирто-воздушной смеси, нагрузки на аппарат, активности железо-молибденового катализатора, температуры и объема теплоносителя, поступающего в межтрубное пространство.
Состав газовой смеси на входе в реактор и на выходе из него иллюстрируется следующими данными.
Табл.1. Состав газовой смеси на входе в реактор
Наименование вещества |
Состав газовой смеси, % мас |
|
вход в реактор |
выход из реактора |
|
азот |
78,79 |
78,82 |
кислород |
8,32 |
4,37 |
вода |
2,21 |
6,36 |
метанол |
8,28 |
0,11 |
формальдегид |
0,31 |
8,06 |
оксид углерода |
0,60 |
0,75 |
диоксид углерода |
0,15 |
0,17 |
аргон |
1,35 |
1,35 |
Результаты промышленной апробации рассматриваемого метода приведены в таблице.
Из нее видно, что предложенный способ получения формальдегида имеет ряд существенных преимуществ по сравнению с известным методом, описанном в [6], в частности, обеспечивает меньшее остаточное содержание метанола в формальдегид-содержащем газе, пониженную норму расхода метанола на тонну карбамидоформальдегидного концентрата КФК-80 и повышенный выход формальдегида.
Табл. 2. Сравнительный анализ работы каталитических аппаратов
Характеристика |
Прототип [6] |
Разработанная конструкция |
Расход катализатора на тонну карбамидоформальдегидного концентрата, кг |
0,07 |
0,07 |
Общая конверсия метанола, % |
99,6 |
99,7 |
Выход формальдегида, % |
92,3 – 93,2 |
94,0 – 94,5 |
Расход метанола на тонну карбамидоформальдегидного концентрата, кг |
652 – 659 |
644 – 647 |
Остаточное содержание метанола в газовой смеси на выходе из реактора, % об. |
0,4 – 0,6 |
менее 0,2 |
Высокая эффективность указанных каталитических аппаратов была подтверждена в ходе длительной эксплуатации инновационных установок получения карбамидоформальдегидного концентрата в ПАО «ТОАЗ». Параллельно с этим удалось существенно улучшить технические и экономические показатели производства формальдегид-содержащего газа и карбамидоформальдегидного концентрата на его основе.
Список литературы.
1.Афанасьев С.В., Махлай В.Н. Введение в химию карбамидоформальде- гидного концентрата. Монография - Тольятти.: ТГУ. 2000 - 114 с.
2. Каталитические процессы в газохимии. Монография. Под ред. д.т.н. С.В. Афанасьева. – Самара.: Изд. СНЦ РАН. 2021. – 244 с.
3.Афанасьев С.В. Инновационные процессы переработки метанола в карбамидоформальдегидный концентрат и продукцию на его основе //Neftegaz. ru. Деловой журнал. 2022. №10. С. 66 – 70.
4. Афанасьев С.В., Махлай С.В. Карбамидоформальдегидный концен- трат. Технология. Переработка. Монография.– Самара.: Изд. СНЦ РАН. 2012.- 298 с.
5.Патент на полезную модель RU №40012. МПК 7 В 01 J /08. Реактор/ В.Н. Махлай, А.В. Макаров, В.А. Семёнова, С.В. Афанасьев и др. Опубл. 2004. Бюл. №24.
6.Сиоли Г., Бианчи Д., Филипчи Е., Зарди Ф. Новые промышленные реакторы для получения производных синтез-газа: аммиака и мочевины, метанола и формальдегида //Химическая промышленность. 1997. №5. С.363-377.
