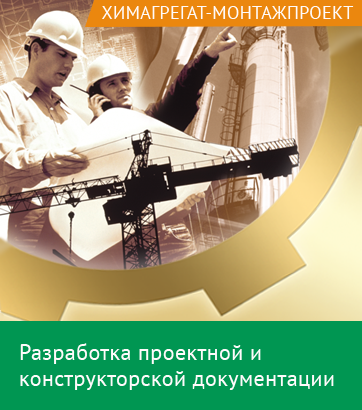
ПРИМЕНЕНИЕ СИСТЕМ КОМПЛЕКСНОГО ДИАГНОСТИЧЕСКОГО МОНИТОРИНГА ДЛЯ ОЦЕНКИ ТЕХНИЧЕСКОГО СОСТОЯНИЯ ОБОРУДОВАНИЯ ХИМИЧЕСКИХ И НЕФТЕПЕРЕРАБАТЫВАЮЩИХ ПРЕДПРИЯТИЙ
А.Н. Мисейко, В.Г. Харебов (ООО «Научно-технический центр «ЭгидА»)
В условиях современной экономики одним из перспективных направлений повышения эффективности управления основными фондами химических и нефтеперерабатывающих предприятий является переход к обслуживанию и ремонту технологического оборудования по фактическому техническому состоянию. Он позволяет увеличить прибыль за счет сокращения простоев оборудования и оптимизации длительности межремонтных периодов, снизить затраты на превентивный ремонт еще работоспособного оборудования, обеспечивает гибкое распределение внутренних ресурсов предприятия, стимулирует поиск и внедрение инновационных технологий обслуживания и ремонта. Однако такой переход предполагает существенное повышение ответственности предприятия в вопросе обеспечения надежной и безопасной эксплуатации оборудования. Особую актуальность эта проблема имеет для нефтеперерабатывающих предприятий, где обращаются пожаро- и взрывоопасные вещества, а аварии и отказы технологического оборудования в результате ухудшения его технического состояния могут привести к многочисленным человеческим жертвам и многомиллионным убыткам, нанести непоправимый урон экологии.
Реализация вышеуказанной концепции ремонта и обслуживания на химических и нефтеперерабатывающих предприятиях невозможна без организации эффективной системы сбора и анализа информации о текущем техническом состоянии технологического оборудования, что, в свою очередь, накладывает определенные требования на способы, методы и средства получения подобной информации.
Система сбора и анализа оперативной информации о текущем техническом состоянии оборудования химических и нефтеперерабатывающих предприятий должна предусматривать следующие виды контроля:
- непрерывный контроль (мониторинг) наиболее ответственного оборудования в процессе эксплуатации;
- периодический контроль менее ответственного оборудования в процессе эксплуатации;
- входной контроль материалов, применяемых при монтаже и ремонте оборудования;
- контроль оборудования после монтажа и ремонта перед допуском в эксплуатацию;
- контроль полноты и правильности действий персонала, ответственного за эксплуатацию и ремонт оборудования.
Важнейшая роль в описанной системе сбора и анализа информации отводится мониторингу технического состояния наиболее ответственного оборудования в процессе эксплуатации, который должен в режиме реального времени решать следующие задачи:
- обнаруживать дефекты, представляющие опасность для целостности и работоспособности эксплуатируемого оборудования;
- определять с необходимой точностью местоположение, тип и характер обнаруженных дефектов;
- адекватно оценивать степень опасности обнаруженных дефектов;
- наблюдать за динамикой развития обнаруженных дефектов и прогнозировать момент перехода оборудования в критическое состояние;
- предупреждать эксплуатационный персонал о приближении критического состояния оборудования и своевременно предотвращать аварийные ситуации путем выработки управляющих воздействий.
Для решения вышеперечисленных задач авторы предлагают использовать системы комплексного диагностического мониторинга (КДМ), основанные на методах неразрушающего и параметрического контроля. Обобщенная функциональная схема предлагаемой системы КДМ для оценки технического состояния химического и нефтеперерабатывающего оборудования приведена на рис. 1. Согласно этой схеме в системе КДМ выделяются измерительная, вычислительная и исполнительная части. Методы и средства, обеспечивающие функционирование каждой из этих частей, варьируются в зависимости от параметров контролируемого оборудования и условий мониторинга. Измерительная часть представлена многофункциональными модулями сбора и обработки данных (МСОД), получающими информацию с диагностических и параметрических датчиков. К первым следует отнести датчики акустической эмиссии (АЭ), вибрации, деформации, скорости коррозии, линейных перемещений, акселерометры, инклинометры и т.п., регистрирующие изменения состояния материала контролируемого оборудования и положения оборудования в пространстве. Ко вторым относятся датчики, регистрирующие параметры эксплуатации оборудования (давление, температуру, уровень рабочей среды и т.п.) и параметры окружающей среды (уровень осадков, температуру воздуха, направление и силу ветра и т.п.). Вычислительная часть состоит из центральной вычислительной станции (ЦВС), устанавливаемой в помещении операторной, а также из промежуточных вычислительных станций, устанавливаемых недалеко от контролируемого оборудования. Исполнительная часть представляет собой запорно-регулирующую арматуру (клапаны, задвижки, заслонки и т.п.), позволяющую управлять режимом работы контролируемого оборудования.
На рис. 2 приведена обобщенная структурная схема предлагаемой системы КДМ технического состояния химического и нефтеперерабатывающего оборудования с различными вариантами построения: 1 – для оборудования, расположенного поблизости от ЦВС; 2 – для группы близко расположенных единиц технологического оборудования; 3 – для протяженного (крупногабаритного) оборудования или единиц оборудования, находящихся на значительном удалении друг от друга и ЦВС.
Рассматривая мониторинг как важнейшую составляющую системы получения оперативной и достоверной информации о текущем техническом состоянии оборудования, следует отметить, что особое значение имеет мониторинг оборудования с критическими дефектами, вынужденно эксплуатируемого по причине неремонтопригодности или невозможности его замены в кратчайшие сроки, а также оборудования, фактические параметры эксплуатации которого превышают проектные значения. Риск отказов такого оборудования несоизмеримо выше, поэтому оно должно быть в первую очередь оснащено системами мониторинга технического состояния.
В качестве примера успешной реализации на практике описанных принципов построения систем КДМ можно привести опыт разработки и внедрения интеллектуальной системы мониторинга технического состояния абсорбера циркулирующего газа К-102 на установке ЛЧ-24/7 ЗАО «РНПК». Указанный абсорбер эксплуатируется с 1970 г. со следующими параметрами: рабочее давление – 4,2 МПа, рабочая температура +45 оС, рабочая среда – 15% раствор моноэтаноламина в смеси с водородсодержащим газом и сероводородом. Абсорбер изготовлен из легированной стали марок 11483.1 и 11474.1 (ЧССР), его толщина составляет 24 мм, внутренний диаметр и высота соответственно равны 1200 и 16450 мм. Верхняя часть абсорбера имела критические дефекты в виде расслоения (площадью около 0,4 м2, глубиной от 6,1 до 12,4 мм) металла днища и трещины (длиной 140 мм, глубиной от 12 до 14 мм) с внутренней стороны абсорбера в сварном шве приварки днища к корпусу. Ремонт этих дефектов с применением сварочных работ был признан нецелесообразным в связи с опасностью последующего коррозионного растрескивания металла абсорбера, а полная замена верхней части в период текущего ремонта являлась невозможной из-за отсутствия необходимых материалов. Поэтому было принято решение об оснащении абсорбера К-102 системой мониторинга для непрерывного наблюдения за динамикой развития имеющихся дефектов в процессе эксплуатации и заменой дефектных элементов при очередном капитальном ремонте установки.
Основным методом контроля технического состояния абсорбера К-102 при построении системы мониторинга был выбран акустико-эмиссионный метод неразрушающего контроля. Он обеспечивает высокую чувствительность к развивающимся дефектам и позволяет выполнять адекватную оценку степени их опасности в режиме реального времени. Кроме того, в число параметров, контролируемых системой мониторинга, были включены давление и температура рабочей среды внутри абсорбера, а также параметры метеорологической обстановки на производственной площадке. Их регистрация необходима для нахождения корреляции с параметрами сигналов АЭ и построения трендов зависимости технического состояния абсорбера от влияния различных факторов.
Технические средства в составе разработанной системы мониторинга по способу и месту установки были разделены на средства измерения, установленные непосредственно на поверхности абсорбера К-102, и оборудование, установленное в помещении операторной.
К средствам измерения, непосредственно установленным на поверхности абсорбера К-102, относились:
- 4 датчика АЭ, расположенные в защитных гильзах, приваренных к корпусу абсорбера;
- 2 МСОД, содержащие аналоговые и цифровые частотные фильтры, усилители, аналого-цифровые преобразователи, цифровые компараторы амплитуды, вычислительные устройства для расчета характеристик сигналов АЭ, а также измерительные каналы токовой петли для регистрации медленно меняющихся параметров (типа давления и температуры) с первичных или вторичных преобразователей, оснащенных токовым выходом 4-20 мА;
- 3 клеммные коробки;
- комплект соединительных кабелей (измерительных линий).
В состав оборудования, установленного в помещении операторной, входили:
- ЦВС, содержащая системный блок, монитор с жидкокристаллическим дисплеем, клавиатуру, мышь, источник бесперебойного питания (ИБП);
- коммутационный шкаф гальванической развязки (КШГР);
- консоль метеостанции;
- комплект соединительных кабелей (измерительных линий).
Сигналы АЭ, возникающие в результате действия эксплуатационных, ветровых нагрузок и осадков регистрировались четырьмя датчиками АЭ, установленными в верхней части абсорбера К-102. Три датчика АЭ были установлены по периметру шва приварки верхнего днища к корпусу абсорбера на равном расстоянии друг от друга и смещены на 200 мм вниз от уровня указанного сварного шва. Один датчик АЭ был установлен на верхнем днище абсорбера.
Каждая пара датчиков АЭ подключалась к многофункциональному модулю МСОД, который обеспечивал гальваническую развязку измерительных каналов, прием аналоговых сигналов с датчиков АЭ и датчиков контроля дополнительных параметров, преобразование их в цифровую форму и последующую обработку. Оба МСОД соединялись одной измерительной линией (кабель типа МКЭШВ 2х2х1,5 мм). Линия подключалась к концентратору, который располагался внутри КШГР, который, в свою очередь, устанавливался в помещении операторной установки ЛЧ-24/7. Концентратор обеспечивал электропитанием подключенные к нему МСОД, принимал и обрабатывал поступающую от них информацию. Кроме концентратора КШГР содержал источники питания класса AC/DC, буферные модули, медиаконвертер, предохранитель, автоматический выключатель, контактор, несущие DIN-рейки, шины заземления, коммутационные клеммы и стопоры. Буферные модули предназначаются для продолжения работы системы мониторинга в течение нескольких секунд после несанкционированного отключения электропитания и корректного завершения ее работы. Предохранитель и автоматический выключатель обеспечивают защиту электрических цепей от перегрузки и короткого замыкания. Контактор обеспечивает коммутацию электропитания при нажатии на кнопку включения/выключения КШГР и разрыв цепи электропитания при его несанкционированном отключении.
С выхода КШГР информация поступала в ЦВС. ЦВС, используя стандартные протоколы обмена, обеспечивал режим удалённого доступа с поддержкой управления и передачи данных. На ЦВС также поступала информация о метеорологических параметрах с метеостанции и об эксплуатационных параметрах с датчиков давления и температуры. Накапливаемая информация сохранялась на жестком диске компьютера в виде базы данных и в любое время могла быть извлечена для последующего анализа технического состояния абсорбера К-102.
Структурная схема разработанной системы КДМ технического состояния абсорбера циркулирующего газа К-102 приведена на рис. 3.
Для вышеописанной системы мониторинга было разработано соответствующее алгоритмическое и программное обеспечение, которое обеспечивало оценку технического состояния абсорбера К-102 в процессе эксплуатации на основании критериев, учитывающих изменение скорости регистрации сигналов АЭ и их основных параметров (амплитуды, энергии, длительности, количества выбросов, времени нарастания и пр.) в зависимости от действия эксплуатационных нагрузок и изменения метеорологической обстановки на производственной площадке.
Обслуживающий персонал установки ЛЧ-24/7 получал оперативную информацию о техническом состоянии абсорбера К-102 в виде цветовых индикаций и сообщений в информационном поле программы на экране монитора ЦВС. Там же отображались рекомендации для обслуживающего персонала.
Программным обеспечением системы КДМ предусматриваются следующие индикации, характеризующие техническое состояние абсорбера К-102:
- индикация «НОРМА» показывает, что система мониторинга функционирует в штатном режиме, техническое состояние абсорбера не ухудшается (информационное поле имеет зеленый цвет);
- индикация «ВНИМАНИЕ» показывает, что система мониторинга зарегистрировала возможность ухудшения технического состояния верхней части абсорбера (информационное поле программы имеет желтый цвет, а в панели сообщений желтым цветом выведена строка «Опасный источник АЭ»);
- индикация «ТРЕВОГА» показывает, что система мониторинга зарегистрировала приближение технического состояния абсорбера к критическому значению, существует возможность разрушения верхней части абсорбера, обслуживающему персоналу выдаются рекомендации по срочному снижению эксплуатационных нагрузок на абсорбер (информационное поле программы имеет красный цвет, а в панели сообщений красным цветом выведена строка «Критический источник АЭ»).
Для повышения надежности функционирования аппаратной части и обеспечения достоверности измерений в установленной системе мониторинга был реализован алгоритм автоматической калибровки датчиков АЭ и самотестирование измерительных каналов. Периоды времени между автокалибровкой и самотестированием задавались программным способом, но автокалибровка проводилась не реже 1 раза в сутки.
Вышеописанная система мониторинга успешно обеспечивала в режиме реального времени безаварийную эксплуатацию дефектного абсорбера К-102 установки ЛЧ-24/7 ЗАО «РНПК» в течение 1,5 лет до момента демонтажа абсорбера и замены его на новый. Применение данной системы мониторинга позволило сэкономить существенные финансовые средства на срочную закупку оборудования под замену, не допустить простоя установки и в то же время обеспечило поддержание промышленной безопасности на необходимом уровне. Опыт ее внедрения и эксплуатации свидетельствует о большой перспективе применения систем подобного класса при переходе на обслуживание и ремонт технологического оборудования химических и нефтеперерабатывающих предприятий по фактическому техническому состоянию. Принципы построения данных систем могут быть широко использованы для организации непрерывного мониторинга технического состояния наиболее сложного и ответственного оборудования предприятий химической и нефтеперерабатывающей промышленности.
