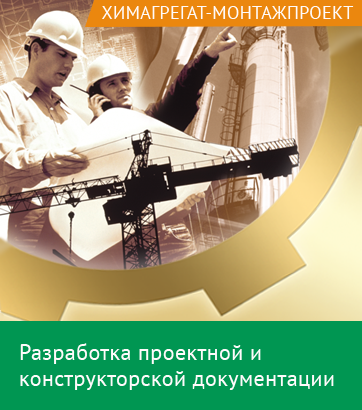
Преимущества применения теплообменного оборудования компании Nexson Group SAS в процессах глубокой переработки нефти
Нугманов Е.Р., технический директор ООО «НЕКСАН РУС», к.т.н
В настоящее время общей проблемой нефтяной отрасли является уменьшение разведанных запасов лёгкой нефти. Запасы нефти, удобные для добычи и переработки, истощаются ускоренными темпами, а практически весь прирост запасов происходит за счет тяжёлой вязкой сернистой нефти. По данным экспертов, мировые запасы тяжелой нефти составляют более 810 миллиардов тонн, и, в недалекой перспективе переработка тяжелой нефти будет расти, а вместе с этим будет расти спрос на технологии её глубокой переработки.
Переработка тяжелой нефти весьма затруднительна, энергоёмка и, как следствие, низкорентабельна и может быть убыточной. Для обеспечения приемлемой глубины переработки такой нефти с помощью известных технологий требуются большие капиталовложения, высокие процентные нормы эксплуатационных затрат и оборотных средств. Всё это в купе с общемировой тенденцией на возобновляемые источники сырья стало основной причиной падения показателей чистой прибыли крупнейших международных нефтяных корпораций, которые были вынуждены пересматривать свои инвестиционные программы в секторе переработки.
В России отрасль нефтепереработки отстает в своем развитии от промышленно развитых стран мира, как и качество выпускаемых нефтепродуктов. Структура производства продукции на российских НПЗ за предыдущие десять лет (2010 – 2020 гг.) хоть и была значительно модернизирована, но всё ещё сильно уступает мировой. Техническое оснащение большинства российских НПЗ не соответствует передовому мировому уровню. В российской нефтепереработке основными проблемами остаются низкая глубина переработки нефти – (в России – 72%, в Европе – 85%, в США – 96%), отсталая структура производства с минимумом вторичных процессов, и недостаточный уровень процессов, улучшающих качество получаемых продуктов. Еще одна проблема – высокая степень износа основных фондов, и, как следствие, повышенный уровень энергопотребления. На российских НПЗ около половины всех печных агрегатов имеют КПД 50- 60% при среднем показателе на зарубежных заводах до 90%. Значения Индекса Нельсона (показатель технической оснащённости НПЗ) для основной массы российских НПЗ ниже среднего значения этого показателя в мире (4,4 против 6,7), что связано с невысокой глубиной переработки нефти, недостаточным уровнем качества нефтепродуктов и технически устаревшим оборудованием. Наиболее развитые на нефтеперерабатывающих заводах в России процессы прямой перегонки нефти и установки, улучшающие качество прямогонных фракций, позволяют получить глубину переработки нефти не более 60%, переработка вакуумного газойля увеличивает глубину переработки до 75-80%, и только переработка гудрона и тяжелых остатков вторичных процессов позволяет перейти рубеж в необходимые в современных условиях 85-90% (Рис.1).
Рис1. Изменение глубины переработки нефти
Единственным выходом из сложившейся ситуации является ускорение модернизации нефтеперерабатывающей промышленности России в направлении строительства установок, углубляющих переработку нефти, важной частью которых является организация эффективного теплообмена. Общая схема процессов глубокой нефтепереработки насчитывает более двадцати основных и вспомогательных установок, на каждой из которой необходимо осуществлять и оптимизировать теплообмен.
Спирально-пластинчатые теплообменные аппараты GreenSpiral™
Для этих целей компания Nexson Group SAS предлагает своим заказчикам передовое теплообменное оборудование – спирально-пластинчатые аппараты GreenSpiral™, которые представляют собой новое поколение компактных спиральных теплообменников, обладающих усиленной и универсальной конструкцией, позволяющей использовать их в самых разных процессах для решения задач теплообмена в условиях повышенной загрязнённости и вязкости рабочих сред.
Зона теплообмена аппаратов GreenSpiral™ состоит из двух концентрических каналов, ширина которых контролируется специальными направляющими и выбирается в соответствии с требованиями Заказчика и условиями эксплуатации. Такой подход к конструированию теплообменного оборудования позволяет учитывать такие параметры как расход сред, наличие и концентрация механических примесей, величина потерь давления. С торцов аппараты закрываются съёмными крышками, что обеспечивает свободный доступ для инспекций и очистки теплопередающей поверхности. А их внутренняя поверхность облицована тем же материалом, что используется для изготовления спиралей. Таким образом все детали аппарата, контактирующие с рабочей средой, устойчивы к её воздействию.
Рис.2а и 2б – Спирально-пластинчатый теплообменный аппарат GreenSpiral™
Спирально-пластинчатые теплообменники GreenSpiral™ рассчитаны для работы с давлениями от полного вакуума до 100 бари, и температурами от -200°C до 450°C. Площадь аппаратов GreenSpiral™ может варьироваться от 1-го до 1000 м2 и более, что позволяет применять их в самых разнообразных процессах и установках.
Эффект самоочистки
Главным преимуществом и уникальной особенностью спирально-пластинчатых теплообменников, выгодно отличающих их от теплообменного оборудования любого другого типа, является «Эффект самоочистки». Это явление достигается благодаря одноканальной конструкции теплообменников, когда в случае работы с загрязнёнными и вязкими средами при формировании отложений на теплопередающей поверхности никакого перераспределения потока жидкости не происходит и поток продолжает своё движение по каналу аппарата на выход. При этом в зоне
Рис.3
формирования отложения в канале теплообменника образуется сужение, и уменьшается площадь его поперечного сечения. Это приводит к возрастанию локальной скорости потока жидкости и увеличению напряжение сдвига в пристеночном слое, что в свою очередь позволяет отложению размываться и уноситься с потоком. Эта особенность позволяет аппаратам GreenSpiral™ эффективно работать длительное время в условиях сильнозагрязнённых и тяжёлых рабочих сред, таких как гудроны и тяжёлые нефтяные остатки, максимально увеличивая межсервисный пробег и минимизируя расходы на обслуживание.
В зависимости от характеристик рабочих сред и условий применения теплообменники GreenSpiral™ могут изготавливаться из различных материалов, таких как: углеродистые стали SA516 gr60, SA516 gr70, нержавеющие стали AISI 304/304L, 316/316L/316Ti, Duplex UNS S31803/S32205, Титан, сплавы SMO254, Hastelloy C-276, C-22, C-2000.
Помимо изготовления теплообменного оборудования, специалисты компании Нексан производят тщательный предварительный подбор параметров теплообменных аппаратов, необходимых для наилучшего решения конкретных задач заказчиков, включая оптимизацию целых теплообменных схем, чтобы максимально использовать достоинства производимого оборудования.
Применение аппаратов GreenSpiral™ в процессах глубокой нефтепереработки на примере установки получения битума
Один из процессов глубокой переработки нефти, связанных с переработкой тяжёлых нефтяных остатков, является процесс производства битума. Наиболее распространённым является способ продувки сырья (как правило, гудрона) воздухом при высоких температурах (220-270°С) в специальной окислительной колонне с получением окисленного битума. Схема процесса достаточно проста и содержит лишь стадию подогрева сырья / охлаждения продукта и стадию окисления (Рис.4).
Рис. 4 – Принципиальная схема получения битума
Данный процесс имеет дело с тяжёлыми вязкими средами, которые способны очень быстро загрязнять стандартные кожухо-трубные теплообменные аппараты. Поэтому решение с использованием оборудования спирально-пластинчатой конструкции GreenSpiral™ для рекуперации тепла отходящего битума, подогрева исходного сырья и особенно финального охлаждения битума является наиболее эффективным и экономически выгодным. Использование аппаратов GreenSpiral™, которые обеспечивают высокую скорость битума в каналах, реализуя эффект самоочистки позволяет значительно снизить степень загрязнения и увеличить межсервисные интервалы для теплообменного оборудования по сравнению с традиционными кожухотрубными аппаратами.
Важным аспектом применения спирально-пластинчатых аппаратов является правильный подбор конфигурации аппарата, которая будет наиболее эффективной в данном конкретном процессе. В связи с этим, специалисты компании Нексан всегда отталкиваются от задачи заказчика и разрабатывают индивидуализированное решение. Часто для этого приходится не просто произвести расчёт теплообменного оборудования, а осуществлять оптимизацию всей теплообменной схемы с учётом тонкостей и особенностей спирально-пластинчатых теплообменников.
Примером такой оптимизации системы теплообмена является проект установки по производству битума, осуществлённый компанией несколько лет назад на одном из крупных российских нефтеперерабатывающих заводов. Основной проблемой, которую было необходимо решить, стал широкий диапазон расходов рабочих сред, который варьировался от минимального к максимальному с разницей в 7-8 раз. Заказчик планировал использовать по одному аппарату на каждую позицию, который должен был обеспечить работоспособность при всех возможных расходах сред, а изначальная схема выглядела следующим образом (Рис.5)
Рис.5 - Первоначальная схема теплообмена установки производства битума
На стадии конкурсных процедур по закупке теплообменного оборудования были проанализированы полученные от заказчика технические задания. На основании результатов анализа полученных исходных данных специалистами компании Нексан были сделаны расчёты и представлено заключение, что выбранное проектно-технологическое решение рассчитано на работу при максимальных режимах нагрузки и не сможет обеспечить непрерывного получения битума на меньших режимах работы при существенном снижении объемов технологических потоков из-за крайне низкой скорости сред, а также сильному изменению температурных графиков из-за чрезмерного запаса поверхности.
Благодаря тесной совместной работе специалистов Нексан, проектного института и проектного офиса заказчика удалось серьёзно модифицировать первоначальную схему, сделав её не просто работоспособной, а невероятно гибкой. Это было достигнуто путём разделения максимально возможного расхода на пять параллельных веток и использование на каждой из них гораздо меньших по габаритам и площади аппаратов, что позволило не просто организовать и максимальный и минимальный режимы в наиболее эффективной конструкции теплообменного аппарата, но и работать на любом расходе во всём диапазоне без ущерба для эффективности и гидродинамических режимов оборудования. В частности, каждая из пяти веток могла эффективно работать при расходах битума в диапазоне 11,5 – 17,5 т/час, обеспечивая максимальный расход 87,5 т/ч при полной загрузке всех пяти веток и достигая всех необходимых температурных параметров. Итоговая принципиальная схема теплообмена установки битума приведена на рис.6.
Рис.6 – Оптимизированная схема теплообмена установки битума
Несмотря на увеличение количества теплообменных аппаратов в системе с планируемых шести до двадцати пяти единиц, CAPEX установки не изменился, а кажущаяся сложность решения на деле обеспечила бесперебойную работу установки на всех режимах работы с достижением всех основных технологических параметров.
Пример оптимизации системы теплообмена битумной установки показывает, что процессы теплообмена и их правильная организация играют одну из ключевых ролей в обеспечении работоспособности и энергоэффективности процессов глубокой нефтепереработки, а от правильности выбора конструкции и характеристик теплообменного оборудования в конечном счёте зависит эффективность и рентабельность всего нефтеперерабатывающего производства.
Данный опыт использования аппаратов GreenSpiral™ для охлаждения битума может быть перенесён на все процессы, связанные с переработкой и получением тяжёлых нефтяных остатков, такие как висбрекинг, замедленное коксование, гидро- и каталитический крекинг, где спирально-пластинчатые теплообменники производства Nexson Group SAS являются не просто высокоэффективной и надёжной альтернативой традиционным кожухотрубным аппаратам, но и, по сути, единственным оптимальным решением для организации теплообмена тяжёлых, высоковязких и содержащих механические примеси рабочих сред.
