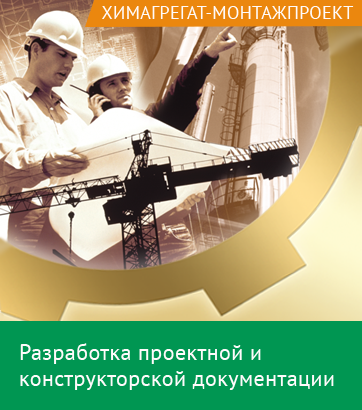
Колонна с вертикальной разделительной стенкой
Яицких Г.С. –Директор по развитию АО «ИПН» Yaitskich@truboprovod.ru
Демченко С.С. –Главный технолог АО «ИПН» Demchenko@truboprovod.ru
Кулаков К.П. – Технический директор АО «ИПН» Kulakov@truboprovod.ru
Степанов Д.Н. – ООО «НОВАТЭК-Усть-Луга» DNStepanov@novatek.ru
В последние годы на многих нефтеперерабатывающих заводах России проводились реконструкции технологических установок с целью повышения производительности и снижения операционных затрат.
Большинство старых технологических установок ЭЛОУ-АТ и ЭЛОУ-АВТ характеризуются низкой степенью рекуперации тепла -40…52% и нередко низким КПД печей - 78…85%. При попытках поднять производительность такой установки даже на 10…20% наблюдается перегрев печей, превышение нормативных показателей температур товарных нефтепродуктов на выходе с установок и значительное превышение удельного расхода топлива и других энергоресурсов.
АО «ИПН» за последние годы разработало и реализовало про-ектно-сметную документацию (ПСД) для реконструкции 12 технологических установок. В результате применения более современного теплообменного оборудования, в частности теплообменников с витыми трубками ООО «СТИМ», эффективных электродегидраторов производства ООО «ЭК ЭИП» и другого технологического оборудования, а также оптимизации схемы теплообмена на основе пинч-анализа, специалистам АО «ИПН» удалось на практике повысить мощность отдельных установок от 30 до 90%(от проектной) без замены печей и ректификационных колонн. На отдельных реконструированных по проектам АО «ИПН» установках удельный расход топлива (на 1 т сырья) был снижен в 1,5…1,9 раза, удельный расход других энергоносителей – от 10 до 30%.
Но применение пинч-анализа и современного технологического оборудования - это не предел возможностей современных инновационных технологий для повышения операционной эффективности как действующих технологических установок, так и вновь строящихся.
Значительные преимущества в достижении дополнительного экономического эффекта в нефте- и газопереработке, а также в нефте- и газо-химии обеспечивает применение колонн с вертикальной разделительной стенкой (Dividing-Wall columns – DWC).
Первые технические решения, связанные с DWC колоннами, были запатентованы в 30-х…40-х годах двадцатого века в Голландии и США, а сегодня в мире эксплуатируются более 100 DWC колонн. Лидером в использовании этого оборудования является фирма BASF (Германия), построившая 70 технологических установок. Самые крупные колонны имеют диаметр 5,2 м и высоту около 100 м.
Также успешно реализуют проекты с использованием этого оборудования зарубежные фирмы Linde AG, Ude, UOP, GTC Techno-logy US LLC, Zehua Company (Китай), а массообменные устройства для колонн поставляют такие известные фирмы, как Sultzer Chemtech, Koch-Glitch, J.Montz GmbH. Например, компания Linde AG разработала для фирмы Sasol DWC колонну высотой 107 м и диаметром 5,2 м для разделения продуктов синтеза Фишера-Тропша.
В настоящее время за рубежом ежегодно вводятся в строй около 5 DWC колонн на различных предприятиях нефтяной и химической промышленности. Применение DWC колонн позволило на практике снизить операционные затраты на 35…40%, капиталовложения в строительство технологических установок на 25…35%; при этом уменьшается площадь застройки - до 40% (в зависимости от схемы установки). Это даёт неоспоримые конкурентные преимущества и значительно повышает экономическую «непотопляемость» таких предприятий даже в самые экономически сложные «турбулентные» времена.
Ниже показаны два частных случая применения DWC колонны [1].
1. Применение DWC колонны в технологическом блоке производства топливного газа (С1, С2), пропана и компонента бензина С4+ из нефтяного газа.
На Рис.1 представлена типовая схема переработки нефтяного газа, применяемая в частности на НПЗ в Техасе (США). В сырье содержится: пропан – 11,8 мас.%, бутанов – 27,9 мас.%, фр. С5+ - 56,6 мас.%. Продукты на выходе с установки: топливный газ, пропановая фракция (содержание С3 не менее 90 мас.%) и компонент бензина С4, С5+.
Рисунок 1 – Типовая схема переработки нефтяного газа
Колонна деэтанизатор 1 работает при высоком давлении 3,2 МПа. Топливный газ (С1, С2, С3) выводится с верха колонны. Из колонны депропанизатора выводится пропан - всего 55% от потенциального содержания в сырье, остальные 45% уносятся с топливным газом - теряется дорогостоящий товарный продукт. При желании, для повышения глубины извлечения пропана из топливного газа (С1, С2, С3) до 94…95% необходимо строить дополнительный блок низкотемпературной сепарации, что удваивает инвестиции в установку переработки нефтяного газа.
На Рис.2 представлена схема переработки нефтяного газа с применением DWC колонны. Верхняя часть колонны разделена на две секции. Первая секция, куда подаётся сырьё, работает как абсорбер, где на внутренних контактных устройствах из восходящего потока топливного газа жидкими углеводородами улавливается пропан. В другой секции верхней части колонны происходит разделение пропана и фракции С4-С5+. Таким образом, в одном корпусе колонны удается совместить два процесса: извлечения ценных компонентов из потока топливного газа и их выделение в товарный продукт.
Сравнительные технико-экономические показатели вышеописанных двух вариантов представлены в Таблице 1.
Таблица 1
№№ п/п |
Показатели |
Единицы измерения |
Типовая схема |
DWC колонна |
1 |
Давление в колоннах |
МПа |
3,2 – деэтанизатор 2,2 - депропанизатор |
2,2 |
2 |
Мощность ребойлера |
МВт |
6,4 |
5,8 |
3 |
Извлечение пропана |
% |
55 |
97 |
4 |
Производство С3 сжиженного |
м3/час |
5,9 |
9,6 |
5 |
Дополнительный объем продаж товарной продукции |
млн. $ США в год |
- |
Плюс 10,2 |
6 |
Экономия капиталовложений |
млн. $ США |
- |
Минус 15,0 |
Рисунок 2 - Схема переработки нефтяного газа с применением DWC колонны
Вариант 2 (DWC колонна) имеет ряд неоспоримых преимуществ по сравнению со старой технологией:
· уменьшается количество единиц технологического оборудования, приборов, трубопроводов и т.п.;
· давление процесса значительно ниже, что снижает стоимость технологического оборудования и операционные затраты;
· значительно снижается энергоёмкость технологического процесса, уменьшается «углеродный след» и штрафы за загрязнение окружающей среды;
· увеличивается отбор дорогостоящего товарного продукта – пропана из топливного газа в 1,76 раза;
· значительно повышаются экономические показатели работы технологической установки.
2. Применение DWC колонны в блоке стабилизации продуктов риформинга бензиновых фракций.
Типовая схема стабилизации продуктов риформинга представлена на Рис.3. Технологическая схема включает колонну-депентанизатор, за ней следует колонна-дебутанизатор и далее – деэтанизатор. Преимущественно С6 и более тяжёлые углеводороды выводятся из кубовой части депентанизатора. В следующей колонне снизу выводится фракция углеводородов С5. В деэтанизаторе поток разделяется на топливный газ и СУГ (сжиженный углеводородный газ). Все три колонны работают под высоким давлением для обеспечения конденсации лёгких фракций, однако значительная часть дорогостоящего СУГ (С3, С4) всё-таки теряется с относительно дешёвым топливным газом (Таблица 2).
Рисунок 3 – Типовая схема стабилизации продуктов рифоминга
На Рис.4 показана альтернативная схема стабилизации продуктов риформинга. DWC колонна выполняет функции деэтанизатора и депентанизатора. Верхняя часть колонны имеет две секции:
· первая секция – это секция абсорбции, где из потока топливного газа извлекаются ценные компоненты (СУГ), абсорбцию производят стабильным риформатом.
· вторая секция – это секция стабилизациии риформата, где из риформата отгоняют углеводороды С3-С5, которые далее разделяют в дебутанизаторе.
Рисунок 4 - альтернативная схема стабилизации продуктов риформинга
Как видно из показателей Таблицы 2, применение DWC колонны в данном случае позволяет:
· значительно сократить количество не только колонн, но и другого технологического оборудования - насосов, теплообменников, кипятильников, трубопроводов, приборов КИП;
· уменьшить капиталовложения и площадь застройки;
· снизить операционные расходы – до 20…24%;
· увеличить производство дорогостоящих продуктов (СУГ, фракция С5) на 54%.
Сравнительные технико-экономические показатели вышеописанных типовой и альтернативной схем приведены в Таблице 2.
Таблица 2
№№ п/п |
Параметры колонны |
Ед. изм. |
Традиционная схема |
Схема с DWC колонной |
|||
депентанизатор |
дебутанизатор |
деэтанизатор |
депентанизатор |
дебутанизатор |
|||
1 |
Количество тарелок |
|
40 |
33 |
27 |
40 |
40 |
2 |
Рабочее давление |
МПа |
1,0 |
1,2 |
3,2 |
0,6 |
1,2 |
3 |
Потребляемая тепловая мощность |
МВт |
43,1 |
2,6 |
0,6 |
33,7 |
|
4 |
Капиталовложения |
млн. $ США |
10,7 |
|
|
8,5 |
|
5 |
Сырье |
т/час |
386,8 |
|
|
386,8 |
|
6 |
С6+ |
т/час |
365,5 |
|
|
365,5 |
|
7 |
С5 |
т/час |
8,1 |
|
|
8,2 |
|
8 |
Топливный газ на выходе |
т/час |
5,8 |
|
|
1,7 |
|
9 |
СУГ |
т/час |
7,4 |
|
|
11,4 |
|
АО «ИПН» имеет большой практический опыт как проектирования новых технологических установок, так и реконструкции старых с применением современных (иногда забытых старых) технических решений и оборудования. Имея все необходимые компетенции, программы и специалистов для возможности использования DWC колонн на вновь строящихся и реконструируемых установках, компания может выполнить:
· разработку ТЭО, или базового проекта для строительства новой или реконструкции старой технологической установки;
· согласовать ТЭО или базовый проект с Заказчиком;
· разработать проектную и рабочую документацию;
· обеспечить сопровождение необходимых экспертиз;
· осуществить авторский надзор за строительством;
· разработать технологический регламент.
Литература:
1.Патент на изобретение RU 2638846 C2 «Процессы разделения с использованием колонн с разделительными стенками».
2. Chemical engineering transaction,vol.69,2018 «Use of Dividing Wall Columns for Process Intensification» GTC Technology US LLC.
