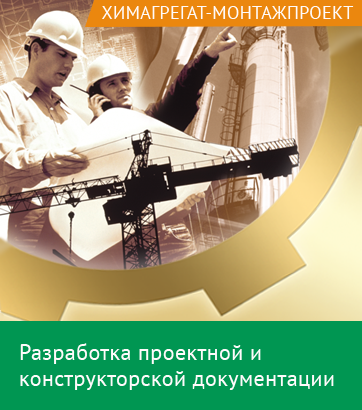
Динамическое моделирование – путь к снижению количества аварийных сбросов от ректификационных колонн
Демченко С.С. – главный технолог АО «ИПН» demcenko@truboprovod.ru
Яицких Г.С. –директор по развитию АО «ИПН» yaitskich@truboprovod.ru
Кулаков К.П. – технический директор АО «ИПН» kulakov@truboprovod.ru
Одной из основных проблем, которая стоит перед проектировщиком при разработке проекта новой установки или реконструкции действующей на взрывопожароопасном производстве - это разработка решений по системе аварийных сбросов (факельной системы). Исходными данными для проектирования новой или разработке решений по модернизации существующей системы аварийных сбросов, выбору новых или поверке существующих предохранительных клапанов является количество сбросов, которое определяется на основе типовых сценариев аварий для основного технологического оборудования.
Основным технологическим оборудованием на нефтеперерабатывающих, нефтехимических и газоперерабатывающих производствах, сброс от которого определяет производительность факельной системы, являются ректификационные колонны.
Расчет количества аварийных сбросов от ректификационной колонны обычно производится методом несбалансированного тепла. Сущность метода заключается в определении количества несбалансированного (избыточного) тепла колонны, которое образуется из-за отказа конденсационного оборудования и/или циркуляционного орошения, и последующем расчете на его основе дополнительно испарившегося количества паров.
Метод несбалансированного тепла является консервативным и приводит к чрезмерному завышению количества аварийных сбросов, что увеличивает капитальные затраты на строительство новых факельных систем или реконструкцию действующих. Основные недостатки метода связаны с допущениями, которые приняты для его реализации:
· фиксированная тепловая нагрузка - постоянство количества тепла, которое вносится с сырьем и в куб колонны;
· составы потоков, входящих и выходящих из колонны, сохраняются такими же, как и при нормальном режиме – отсутствует учет изменения количества выкипающих веществ, при изменении давления и температуры (количество относительно легких фракций остается неизменным);
· постоянство температуры сброса;
· постоянство теплоты испарения и других теплофизических свойств;
полное отсутствие возможности учета конструкции оборудования и его влияния на количество сброса, например, АВО продолжает охлаждать пары верха колонны даже при остановленных вентиляторах за счет естественной конвекции и большой поверхности теплообмена.
Часть недостатков метода несбалансированного тепла можно нивелировать, используя статическое моделирование для режимов аварийного сброса. То есть создавать отдельные статические модели для каждого аварийного случая. По опыту АО «ИПН» такой подход позволяет снизить расчетное количество сбросов на 20-30%.
Динамическая модель же полностью лишена указанных выше недостатков метода несбалансированного тепла, что позволяет с ее помощью оценить, например, такие факторы как частичная потеря тепловой нагрузки ребойлера из-за снижения полезной разности температур между теплоносителем и кубовым продуктом.
Специалистами АО «ИПН» был выполнен сравнительный расчет количества аварийного сброса от колонны разделения бутанов по методу несбалансированного тепла с использованием статического моделирования и динамической модели. При разработке динамической модели были учтены следующие данные:
· конструкция колонны и внутренних контактных устройств – учет количества жидкости и паров, находящихся в колонне;
· конструкция теплообменных аппаратов (конденсационная аппаратура и термосифонные ребойлеры);
· конструкция емкости орошения;
· расходные характеристики насосного оборудования;
· расходные характеристики регулирующих клапанов;
· компоновка оборудования;
· трубопроводная обвязка.
Принципиальная схема работы колонны разделения бутанов представлена на рисунке 1.
Сырье, смесь бутанов, подается в середину колонны. С верха колонны выводится изобутан, с куба колонны выводится н-бутан. Подвод тепла в колонну осуществляется с помощью двух термосифонов.
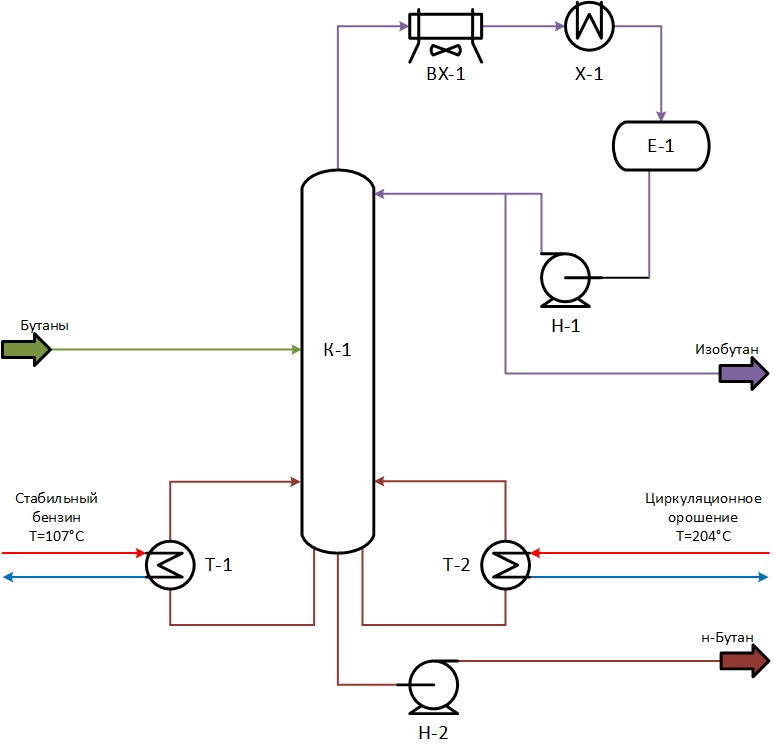
Рисунок 1. Принципиальная схема работы колонны разделения бутанов
Термосифон Т-1 подогревается потоком стабильного бензина с температурой 107°С, термосифон Т-2 подогревается потоком циркуляционного орошения с температурой 204°С.
Для данной колонны аварией с наибольшим количеством сброса является ситуация связанная с потерей орошения. Метод несбалансированного тепла с использованием статического моделирования для данного случая дает количество сброса 32000 кг/ч.
С помощью динамической модели можно получить не только реальное численное количество аварийного сброса, но также проанализировать развитие аварии во времени и оценить влияние различных факторов на развитие аварии.
На рисунке 2 показаны зависимости роста давления в колонне и количества аварийного сброса от времени протекания аварии (потери орошения колонны). Из данных на рисунке 2 видно, что повышение давления в колонне не происходит сразу после потери колонной орошения, так как система имеет определенную емкость (инертность). Рост давления начинается спустя четыре минуты после начала развития аварии, а сброс через предохранительный клапан начинается только с седьмой минуты. То есть можно сделать вывод, что с учетом реального размера системы у персонала будет порядка семи минут, чтобы восстановить подачу орошения и предотвратить дальнейшее развитие аварии. По данным рисунка 2 можно определить максимальное количество сброса, оно составляет 25600 кг/ч, что на 20% меньше количества сброса полученного по методу несбалансированного тепла с использованием статического моделирования. Если же для метода несбалансированного тепла не применять статическое моделирование, то снижение сброса при использовании динамической модели составит до 50%. Данный факт особенно актуален при проведении работ по модернизации действующих производств, которые были запроектированы до масштабного внедрения в процесс проектирования программ моделирования технологических процессов.
Рисунок 2. Зависимости роста давления в колонне и количества аварийного сброса от времени протекания аварии
Динамическая модель также дает ответ на вопрос, почему величина сброса уменьшилась на 20%?
На рисунке 3 показаны зависимости изменения температуры куба колонны и полезной разности температур (LMTD) для теплообменников Т-1 и Т-2 от роста давления в колонне.
Из данных рисунка 3 мы можем увидеть, что с ростом давления в колонне происходит рост температуры в кубе (рост давления приводит к росту температуры кипения н-бутана). С ростом температуры в кубе колонны происходит снижение полезной разности температур в теплообменниках Т-1 и Т-2, то есть снижение движущей силы процесса теплопередачи, а это значит, что через ту же поверхность теплообмена количество передаваемого тепла будет меньше. Снижение тепловой нагрузки на теплообменники Т-1 и Т-2 с ростом давления показано на рисунке 4. Количество аварийного сброса для данной колонны прямо связано с тепловой нагрузкой на термосифоны. При снижении нагрузки на термосифоны происходит и снижение количества аварийного сброса.
Таким образом, динамическая модель позволила учесть влияние характеристик реально установленного оборудования на величину аварийного сброса.
Рисунок 3. Зависимости изменения температуры куба колонны и полезной разности температур (LMTD) для теплообменников Т-1 и Т-2 от роста давления в колонне
Рисунок 4. Зависимость изменения тепловой нагрузки Т-1 и Т-2 от роста давления в колонне
Следует сказать, что динамическая модель позволяет учесть не только влияние характеристик оборудования на величину аварийного сброса, но также и работу автоматизированной системы управления технологическим процессом (АСУТП). Например, если для рассматриваемой колонны подвод теплоносителя в Т-2 осуществлять не по расходу (постоянный расход), а в зависимости от температуры в кубе колонны, то расчетная величина аварийного сброса резко уменьшится, так как с ростом температуры в кубе из-за роста давления, АСУТП будет уменьшать расход теплоносителя в термосифон Т-2. На рисунке 5 представлена зависимость роста давления в колонне и количества аварийного сброса от времени протекания аварии с учетом работы системы АСУТП.
Рисунок 5. Зависимости роста давления в колонне и количества аварийного сброса от времени протекания аварии с учетом работы системы АСТУП
Из данных на рисунке 5 видно, что при учете работы системы АСУТП величина сброса составляет 7800 кг/ч или на 75% меньше от рассчитанного по методу несбалансированного тепла.
Опыт АО «ИПН» по разработке динамических моделей колонн на установках АТ, АВТ, стабилизации и четкой ректификации бензинов, газофракционирования показывает, что стандартные, общепринятые сценарии не всегда приводят к развитию аварии. Таким образом, динамическое моделирование позволяет ответить и на качественный вопрос – а будет ли авария?
Выводы:
Динамическое моделирование позволяет снизить количество аварийных сбросов от колонного оборудования на 20-75% по сравнению с методом несбалансированного тепла.
Для новых установок динамическое моделирование позволяет снизить капитальные затраты на системы аварийного сброса начиная с предохранительных клапанов и заканчивая факельными установками.
Для действующих установок динамическое моделирование позволяет провести техническое перевооружение по увеличению производительности без замены предохранительных клапанов и реконструкции системы аварийного сброса.
