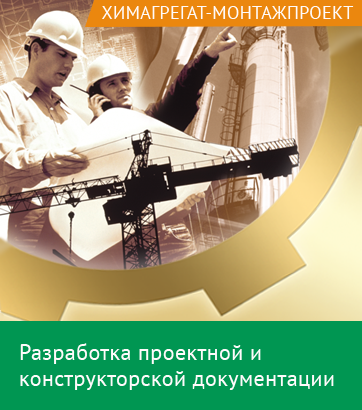
АППАРАТУРНОЕ ОФОРМЛЕНИЕ СОВРЕМЕННОЙ УСТА-НОВКИ ПОЛУЧЕНИЯ МЕТАНОЛА
С.В. Афанасьев, к.х.н., д.т.н.. доцент по специальности «Экология», начальник управления АО «ТОАЗ» по разработке инноваций и их патентованию
Согласно литературным данным, синтезу метанола из природного газа предшествует стадия образования водорода и оксида углерода. Технологический процесс является достаточно сложным, и осуществляется в жаростойких катализаторных трубах печи риформинга, в которых могут быть реализованы три метода окислительного превращения метана в синтез-газ:
- паровая конверсия CH4 + H2O → CO + 3H2 (1)
- парциальное окисление кислородом CH4 + 0,5O2 → CO + 2 H2 (2)
- углекислотная конверсия CH4 + CO2 → 2CO + 2H2 (3)
Наибольшее распространение получили первый и третий методы [1].
Известен [GB №1159095, МПК С 07 С32/00, заявл. 18.08.65 г., опубл. 23.07.69 г.] способ получения метанола, включающий реакцию оксидов углерода с водородом под давлением 1,0 – 15,0 МПа (предпочтительно от 4,0 до 8,0 МПа), при температуре 160 - 300 0С (предпочтительно от 190 до 270 0С ), объёмной скорости 7000 - 25000 ч-1 в присутствии катализатора, содержащего оксиды меди и цинка и, по крайней мере, один трудно - восстанавливаемый оксид металла второй - четвертой групп периодической системы элементов Д. И. Менделеева, выделение метанола из реакционной смеси и рециркуляцию непрореагировавших в синтезе метанола веществ. В качестве сырья применяют смесь водорода с оксидом и диоксидом углерода, в которой содержание СО2 варьирует в интервале 1 - 20 об. % (предпочтительно 3 - 12 об. %). В синтез-газе, контактирующим с катализатором, объёмное отношение водорода к сумме оксидов углерода в 1,3 - 3,0 раза больше стехиометрического.
К недостаткам данного способа следует отнести пониженную удельную производительность медно-цинкового катализатора, а также высокие энергетические затраты на рециркуляцию газовой смеси.
В патентной литературе описан также и промышленный способ получения метанола [RU №2181117 Способ получения метанола. МПК С 07 С 29/154, С07С 31/04. Заявка №99120250/04 от 22.09.1999, опубл. 10.04.2002. Бюл. №20] контактированием газовой смеси, содержащей оксиды углерода и водород, с медьсодержащим катализатором при температуре 190 - 290 0С, давлении 5,0 - 10,0 МПа и объёмной скорости 4500 - 100000 ч-1, причём исходную газовую смесь, содержащую 1,0 – 33,7 об. % оксида углерода, 0,3 - 22,5 об. % диоксида углерода при объёмном отношении водорода к сумме оксидов углерода, равном 1,91 – 5,60, а также 0,5 - 50 об. % азота, последовательно пропускают через каскад проточных реакторов трубчатого типа в одну стадию, а метанол и воду отделяют после каждого реактора.
Рассматриваемый каскадный способ позволяет существенно повысить удельную производительность катализатора, однако его реализация сопряжена со значительными материальными затратами и технически сложна. Кроме того, при его осуществлении возможно существенное снижение срока эксплуатации медно-цинкового катализатора, а производительность метанольной установки пропорциональна количеству проточных реакторов.
Более перспективным по технической сущности является способ получения метанола контактированием газовой смеси, содержащей оксиды углерода и водород, с медно-цинковым катализатором при температуре 200 - 290 0С, давлении 5 - 15 МПа и объёмной скорости 3000 - 10000 ч-1 , отличающийся тем, что конвертированный газ состава, об. %: Н2 - 64,0 ÷ 75,5; Аr - 0,02 ÷ 0,08; N2 - 0,05 ÷ 2,0; СH4 – 1,0 ÷ 3,6; СО – 10,7 ÷ 19,4; СО2 - 3,3 ÷10,4, подаваемый с печи риформинга с объёмной скоростью 800 ÷ 2000 ч-1, предварительно смешивают с диоксидом углерода в объёмном соотношении (3 - 100): 1 и вместе с газами циркуляции пропускают последовательно через 4 катализаторные зоны горизонтального реактора при их объёмном соотношении (1,20 - 1,40): (0,85 - 0,95): (0,9 - 1,2): (0,9 - 1,1), разделённые двумя котлами и одним теплообменником, с выделением метанола по общепринятому методу [RU №2331625. Способ получения метанола. МПК С07С 31/04; С07С 29/151. Заявка №2006106110 от 20.02.2006, опубл. 20.08.2008. Бюл. №23].
В процессе исследования данного способа было установлено, что при прохождении синтез-газа через секции горизонтального реактора уже в первых трёх устанавливается кинетическое равновесие. По указанной причине четвёртая катализаторная корзина незначительно влияет на производительность агрегата. Соответственно, снижается удельный съём метанола с единицы объёма загруженного в реактор катализатора [2;3].
На основании изложенного были выполнены работы по совершенствованию действующей технологической схемы получения метанола.
Поставленная задача реализована тем, что метанол синтезируют контактированием газовой смеси, содержащей оксиды углерода и водород, с медно-цинковым катализатором при температуре 220 - 290 0С, давлении 2 ÷ 12 МПа и объёмной скорости 3000 ÷15000 ч-1. При этом согласно предлагаемому решению, для получения газа состава, об. %: Н2 - 62,0 ÷ 75,0; Аr - 0,04 ÷ 0,20; N2 - 0,07 ÷ 3,0; СH4 – 0,8 ÷ 4,0; СО – 7,8 ÷ 20,0; СО2 - 3,7 ÷ 11, предварительно смешивают природный газ и диоксид углерода в соотношении (3 – 50) : 1 и подают в печь риформинга с объёмной скоростью 800 - 2500 ч-1 . Образующийся синтез-газ вместе с газами циркуляции первого потока пропускают последовательно через три катализаторные зоны горизонтального реактора, разделённые двумя котлами, а во второй циркуляционный поток вводится диоксид углерода при объёмном соотношении (5 – 50) : (0,5 – 2), который после подогрева в теплообменнике поступает в односекционную зону каталитического реактора с выделением метанола из двух технологических линий путём охлаждения реакционных газовых потоков и отделения метанола-сырца в сепараторе [RU №.2698200. Способ получения метанола. МПК СО7С 29/152; СО7С 29/154; СО7С 31/04; С01В 3/32. Заявка №2018142942 от 04.12.2018, опубл. 23.08.2019. Бюл. №24].
В сравнении с другими способами, усовершенствованная технология характеризуется следующими преимуществами:
-в качестве реактора используют аппарат горизонтального типа, разделённый встроенным теплообменником на две изолированные части в соотношении 3 : 1 по количеству катализаторных секций;
-конвертированный газ состава, об. %: Н2 - 62,0 ÷ 75,0; Аr - 0,04 ÷ 0,20; N2 - 0,07 ÷ 3,0; СH4 – 0,8 ÷ 4,0; СО – 7,8 ÷ 20,0 ; СО2 - 3,7 ÷ 11 , синтезируется пропусканием через реакционные трубы печи риформинга смеси природного газа и диоксида углерода, взятых в объёмном соотношении (3 - 50) : 1;
-циркуляционный газ, выходящий из сепаратора после выделения метанола делится на два потока: первый смешивается с синтез - газом и направляется в часть реактора с тремя последовательно расположенными катализаторными секциями, а второй предварительно обогащается диоксидом углерода до соотношения (5 – 50) : (0,5 – 2) и после подогрева газовой смеси во встроенном теплообменнике поступает во вторую часть реактора с одной катализаторной секцией.
При реализации предлагаемого технического решения также принято во внимание, что переработка синтез - газа с содержанием оксида углерода более 30 об. % и азота свыше 20 об. % - неэкономична. По указанной причине в предлагаемом способе используется синтез - газ, в котором дозировки СО и N2 поддерживаются ниже 20 об. %, а объёмное отношение Н2/(СО + СО2) находится в интервале от 2 до 5. Важно отметить, что для протекания последовательных реакций.
СО + Н2О → СО2 + Н2 (4)
СО2 + 3Н2 → СН3ОН + Н2О (5)
с требуемой скоростью оптимальные концентрации СО и СО2 должны находиться в интервале 5 – 20 об. %.
Для достижения указанной дозировки СО2 использована подпитка циркуляционного газа с повышенной концентрацией метана чистым диоксидом углерода [4;5].
Ограничение верхнего предела по СО2 в синтез - газе объясняется возможностью протекания побочных химических реакций и, как результат, снижением количества образующегося метанола.
Для предотвращения накопления инертов в циркуляционном газе предусмотрен вывод его части из системы и сжигание в качестве топлива в печи риформинга.
На рис. 1 приведена принципиальная технологическая схема процесса, а на рис. 2 устройство модернизированного горизонтального реактора.
Рисунок 1.
Конвертированная смесь, полученная в печи риформинга из смеси природного газа и диоксида углерода, взятых в объёмном отношении 5 : 1, подается на всас компрессора 1, охлаждается в воздушном холодильнике 2 и поступает в сепаратор 3 с целью отделения влаги. Осушенный синтез-газ компримируется до заданного давления, подогревается с циркуляционным газом потока I в рекуперативных теплообменниках 4/ и 4 соответственно и обе смеси поступают в горизонтальный реактор 8 в трёхсекционную зону (Рис.2). Поток II циркуляционного газа обогащается диоксидом углерода и направляется на дополнительный нагрев во встроенный теплообменник 12 и далее во вторую односекционную катализаторную часть реактора.
Рисунок 2.
Выходящие из трёхсекционной и односекционной частей аппарата метанол – содержащие газообразные продукты последовательно охлаждаются потоками синтез - газа и циркуляционного газа в рекуперативных теплообменниках 4/ и 4, в воздушном холодильнике 5 и холодильнике - конденсаторе 6 и направляются в сепаратор 7 для отделения метанола – сырца.
В трёхсекционной каталитической зоне реактора установлены два котла для поддержания оптимального температурного режима. Загрузка катализатора осуществляется через люки 9, подача газовых смесей в катализаторные секции регулируется задвижками 10 и клапанами 11.
В качестве катализатора синтеза метанола использован продукт в виде цилиндрических таблеток диаметром 5,2 мм и высотой 5,4 мм, имеющих состав, мас. %: СuО - 64; ZnO - 24; Аl2O3 -10; оксиды других металлов - 2. Его объёмная загрузка в секции реактора по ходу движения синтез-газа иллюстрируется следующими данными, м3:
-трёхсекционная часть аппарата: первая – 29,8; вторая – 21,6; третья – 23,8;
-односекционная часть, следующая за встроенным теплообменником 12 – 23,8.
Подавая в неё циркуляционный газ, обогащаемый вводом диоксида углерода, удаётся сместить равновесие реакции (5) в сторону образования дополнительных количеств метанола. Тем самым решается важная технологическая задача, как повышение съёма метанола с единицы объёма загруженного катализатора.
В таблице приведены данные, получаемые по примерам осуществления предлагаемого способа. Из неё видно, что при смешении синтез-газа с циркуляционным потоком резко снижается объёмная концентрация оксида углерода в газовой смеси и возрастает количество метана. По указанной причине добавление второй части диоксида углерода в циркуляционный газ перед его входом в односекционную часть реактора смещает равновесие реакции (3) в сторону образования оксида углерода, а реакции (5) - к метиловому спирту.
Достигаемый технический результат зависит от объёмного отношения в потоке II циркуляционного газа к введённому в него диоксиду углерода, что иллюстрируется данными таблицы.
Вывод. Реализация предлагаемого инновационного технического решения позволяет оптимизировать технологическую схему процесса, существенно повысить съём метанола с единицы объёма загруженного катализатора, увеличить срок службы каталитической системы.
Список литературы.
1.Афанасьев С.В. Инновации и «зелёные технологии» в газохимии и нефтедобыче. Монография. Под ред. к.х.н., д.т.н. С.В. Афанасьева. – Самара.: Изд. СНЦ РАН. 2022. – 198 с.
2.Патент РФ на полезную модель №44066. МПК В01 J 8/08. Реактор синтеза метанола/ С.В. Афанасьев и др. Заявка №2004129829/22 от 12.10.04, опубл. 27.02.05. Бюл. №6.
3.Афанасьев С.В., Садовников А.А., Гартман В.Л., Обысов А.В., Дульнев А.В. Промышленный катализ в газохимии. Монография. Под ред. д.т.н. С.В. Афанасьева. – Самара.: Изд. СНЦ РАН. 2018. – 160 с.
4.Афанасьев С.В. Инновационные приёмы снижения «углеродного следа» на примере АО «ТОАЗ». Сборник докладов научно-практической конференции Роспатента. «Рынок интеллектуальной собственности как основа инновационного сценария развития экономики России». 20 марта 2024 г. М.; ФИПС. С.6 – 11.
5.Афанасьев С.В., Садовников А.А., Гартман В.Л., Обысов А.В., Дульнев А.В. Каталитические процессы в газохимии. Монография. Под ред. д.т.н. С.В. Афанасьева. – Самара.: Изд. СНЦ РАН. 2021. – 244 с.
