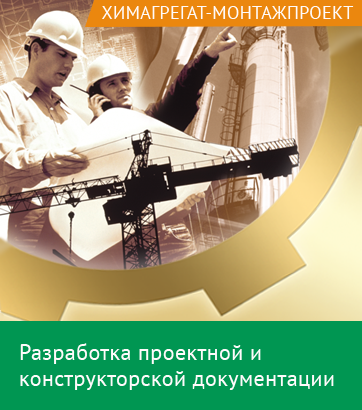
КАО «Азот»: работать на опережение
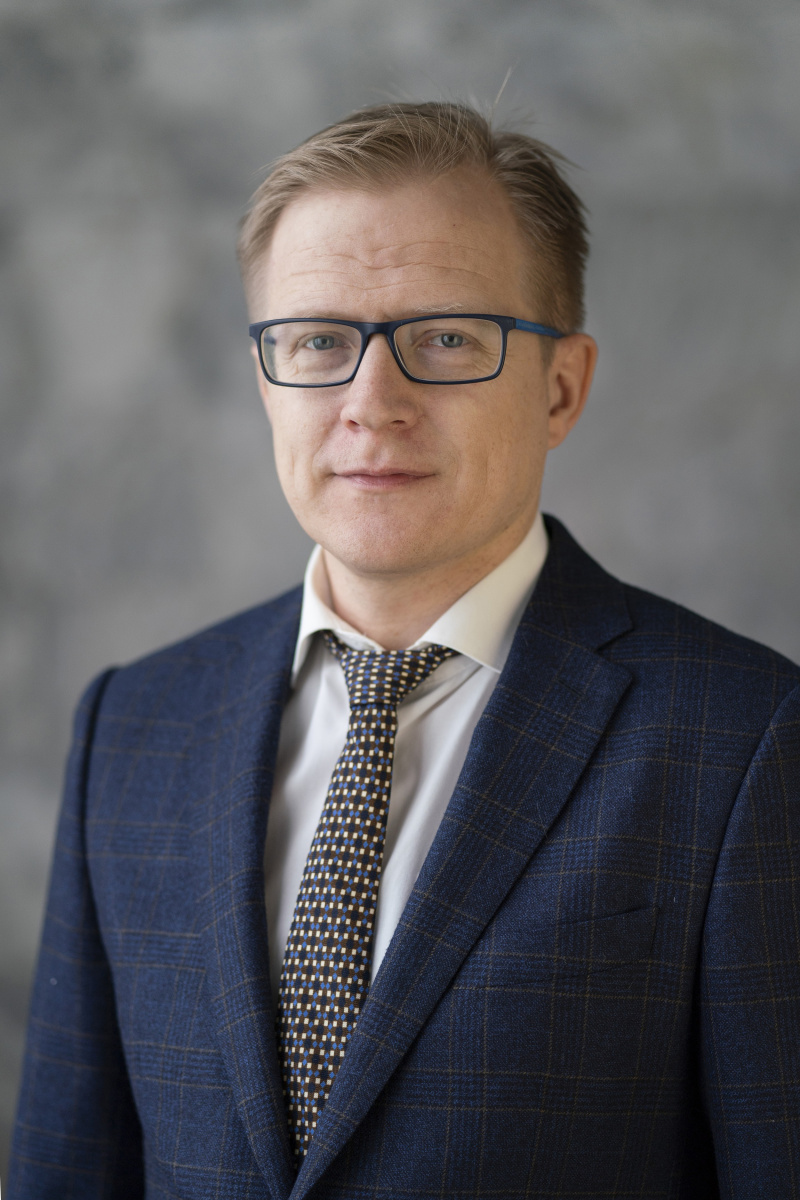
Предприятие КАО «Азот», г. Кемерово, входит в состав АО «СДС Азот» - крупнейшего производителя азотных удобрений в России, основного поставщика аммиачной селитры промышленного применения горнодобывающим предприятиям Сибири и Дальнего Востока. Кемеровский «Азот», давший первую продукцию в 1956 году, сегодня активно развивается, реализуя крупный проект строительства нового комплекса азотных удобрений. В его составе запланирован ряд установок, в том числе, производства аммиака суточной мощностью 2 тысячи т и азотной кислоты на 1,2 тысячи т; получения раствора аммиачной селитры в объеме 1,25 тысячи т и производства пористой аммиачной селитры – 1 тысяча т. Кроме того, будет построено производство карбамида на 2,2 тысячи т в сутки и сульфат нитрат аммония.
Сегодня мы беседуем с человеком, в чьем ведении находятся производственные мощности огромного предприятия, их настоящее и будущее. Знакомьтесь, Андрей Николаевич Вишневский – первый заместитель генерального директора — главный инженер КАО «Азот».
- Повлияла ли сегодняшняя обстановка на планы компании по ремонту и модернизации производства и, в частности, на сроки реализации проекта строительства двух установок мощностью по 500 тонн моногидрата в сутки на промышленной площадке цеха №15 КАО «Азот»?
Получить продукцию с нового агрегата кислоты мы планируем 1 ноября этого года. Сложная ситуация в мире, связанная с пандемией, привела к тому, что ряд европейских заводов, на которых идет изготовление оборудования, остановились. Предприятия должны запуститься в мае, а это сдвигает срок поставки оборудования на два месяца. А также есть задержки по поставке оборудования из США, Индии, Китая. При этом если карантин будет продлен, график пуска агрегата сдвинется на 28 декабря этого года. Но мы продолжаем работу над оптимизацией сроков строительства для того, чтобы запустить объекты в срок.
Капитальные ремонты также оптимизированы, пересмотрены сроки ремонтов в сторону уменьшения. Причина та же, пандемия, срыв сроков поставок оборудования из Франции для ремонта цеха карбамида. Работы перенесены на следующий год.
- Кто создавал данный проект, каков процент использования в нем отечественного и импортного оборудования по разным группам?
Лицензиаром технологии получения азотной кислоты является американская компания KBR. Переработкой проекта с привязкой к требованиям российского законодательства занимается ООО «Промстройинжиниринг» (г. Москва). Генеральный подрядчик строительства — компания «Стэп» (г. Санкт-Петербург). Лицензиаром технологии получения водорода является немецкая компания Linde. Привязку проекта к производственной площадке ведет Проектное управление Кемеровского «Азота». Проект по модернизации цеха аммиачной селитры выполняет московский «ГИАП».
Если говорить о соотношении отечественного и импортного оборудования, то в рамках азотной кислоты это 30/70. Все лицензионное оборудование поставляется из-за рубежа. Приборы КИП и автоматики производятся на локализованных в России заводах, но они принадлежат зарубежным компаниям.
Водородная установка — модульная, полностью изготовлена за рубежом. Все емкостное и насосное оборудование по проекту технического перевооружения аммиачной селитры изготовлено в России, а производители КИП и автоматики — зарубежные компании.
— Как построена эксплуатационно-ремонтная служба предприятия, оборудования, практикуется ли остановка на капремонт всего предприятия, каков межремонтный пробег и актуально ли для Вас его увеличение?
Ежегодно магистральный газопровод, по которому подается природный газ на предприятие, останавливается на четверо суток. Это связано с профилактическими работами у поставщика газа. Соответственно, мы в этот момент вынуждены останавливать свой завод полностью. Всю свою ремонтную кампанию мы строим исходя из этого ограничения. Плановый ремонтный цикл агрегатов крупнотоннажной группы выстроен по принципу 28-8. Один год ремонт составляет 28 дней, следующий — 8 дней. Таким образом, крупные ремонты проводим по двухгодичному циклу. А на перспективу мы уже согласовали с газовиками, что они вместе с нами перейдут на двухгодичный цикл ремонта своих газопроводных магистралей. Так мы сможем полноценно перейти на ремонт оборудования предприятия по двухгодичному циклу. Тема увеличения пробегов, конечно же, для нас актуальна, но ко всему нужно подходить разумно. Пробег должен быть обоснован, потому что потери от внеплановых остановок могут превзойти эффект от увеличения пробега оборудования. Есть еще одно ограничение, которое нельзя не учитывать при организации ремонтных работ, это требование федеральных норм и правил, соблюдение сроков проверок и экспертиз. И здесь основные сложности. Работу в этом направлении ведем совместно с РАПУ, сформированы предложения по изменению подхода к проверкам, изменению их сроков. Совместные предложения направлены на рассмотрение в федеральные органы.
– Как Вы относитесь к выведению механических служб на аутсорсинг? Довольны ли уровнем квалификации сотрудников подрядных организаций?
У нас аутсорсинга нет. Все подразделения находятся внутри структуры предприятия. Попытки вывести подразделение на аутсорсинг предпринимались в конце двухтысячных годов. Был создан так называемый «Азот Сервис». В «Азот Сервис» были выведены все сервисные службы предприятия. В 2013 году было принято решение вернуть все службы в состав предприятия, на тот момент они работали неэффективно.
Что касается подрядных организаций, то на сегодняшний день для нас это одно из самых больных мест. В регионе не так много квалифицированных подрядных организаций, способных выполнять ремонтные работы на крупнотоннажных агрегатах, организаций, допущенных к выполнению работ на опасных производственных объектах. Компании, которые на сегодня имеют специалистов высокой квалификации и необходимую технику, за свои услуги просят довольно дорого, поэтому здесь мы балансируем по принципу цена-качество. Длительное время у нас ничего не строилось, не проводились модернизации, поэтому квалифицированный подрядчик ушел в другие регионы, перешел на вахтовый метод работы. Ряд подрядчиков распустили свой персонал и оставили минимальное количество сотрудников. Так как ремонты проводятся один раз в год, нам необходимо одновременное привлечение большого количества квалифицированных специалистов, с этим есть проблемы. Мы развиваем свою ремонтную службу, набираем в нее персонал, работаем над повышением производительности труда, будем снижать свою зависимость от подрядных организаций.
– Идет ли внедрение «цифры» в практику ремонтно-механических служб, и каковы дальнейшие перспективы цифровизации на КАО «Азот»?
Цифровизация, конечно, наступает, точнее, мы сами зовем ее к себе, и ремонтно-механическая служба не исключение. Внедрение автоматизированной системы управления активами на основе рисков, электронные обходы, электронные наряды допуска, прогнозная диагностика, электронные системы предсменного тестирования, цифровые модели и двойники — это небольшой перечень проектов, которые сейчас реализуются на предприятии. Мы уже сейчас по ряду подразделений видим ежедневную расстановку людей по работам, их загрузку, исполнение сменных заданий, исполнение программы обходов, реакцию руководителей на выявленные замечания. Мы поставили перед собой задачу достичь общей эффективности работы оборудования на уровне 95%. Внедрение цифровых технологий является неотъемлемой частью этой стратегии.
– Насколько нам известно, каждый новый объект еще на этапе проектирования сопряжен с вопросами экологии и проходит целый ряд обязательных процедур. Расскажите, как все это было на примере конкретного проекта по строительству двух установок мощностью по 500 тонн моногидрата в сутки на промышленной площадке цеха №15 КАО «Азот».
Мы проходили все в полном соответствии с законодательством, были общественные слушанья, экологическая экспертиза, главгосэкспертиза, получение разрешение на строительство. Единственное, не смогли пройти экологическую экспертизу с первого раза, потому что возникли определенные вопросы к технологии, которую мы применяем: ее на настоящий момент в Российской Федерации нет. Нам не давали экологическую экспертизу до того момента, пока мы не доказали, что данная технология является безопасной. Мы собирали дополнительные документы, обоснование и повторно выходили на экологическую экспертизу, со второго раза прошли ее успешно.
– Как удается такому крупному и сложному химическому предприятию успешно решать множество самых разнообразных вопросов, связанных с экологией?
Мы поднадзорное предприятие, опасный производственный объект, оказывающий негативное воздействие на окружающую среду. Мы действуем в соответствии с законодательством, и работа по вопросам экологии построена системно. В КАО «Азот» уже на протяжении многих лет функционирует экологический отдел. Главными его задачами являются получение разрешительной документации для предприятия и соблюдение природоохранного законодательства в структурных подразделениях. Все вместе мы работаем на опережение, тем самым исключая риски по претензиям со стороны надзорных органов.

- Какие проблемы, на Ваш взгляд, являются наиболее сложными и хлопотными для главного эколога предприятия: учет выбросов разного рода, взаимодействие с коллегами и руководством производства, с общественностью или с госорганами?
Предприятие расположено в черте города, санитарно-защитная зона граничит с жилой застройкой, завод имеет более 500 источников выбросов, более 100 наименований отходов и потому находится на постоянном контроле у администрации города. На сегодня экологические показатели нашей работы по агрегатам аммиака выведены напрямую губернатору Кузбасса. Это большая ответственность, эколог всегда на острие. Все должно быть в порядке: и отчеты, и показатели, и все в срок, все вовремя. Найти общий язык со всеми, с администрацией, с цехами, Росприродназором — это непростая задача, но сегодня наш эколог с ней справляется хорошо. Не могу выделить, что из этого наиболее сложно и хлопотно, думаю, все.
— Устраивает ли Вас то, как построено и работает законодательство в экологической сфере, система получения разрешительной документации?
Изменения основного закона об охране окружающей среды ФЗ №7, внесенные 21.07.2014, серьёзно скорректировали работу хозяйствующих субъектов на территории РФ. Появились новые требования, в большей части более жесткие в отношении соблюдения норм и правил.
Требования законодательства в экологической сфере обширны, в некоторых случаях несопоставимы друг с другом, что приводит к неопределенностям в выстраивании хозяйственных отношений между юридическими лицами. Несмотря на это, есть и положительные моменты, например, создание такого программного продукта для природопользователей, как «Личный кабинет природопользователя». Наличие личного кабинета упростило нам процедуру подачи отчетности или документов для получения разрешительной документации в электронном виде с ЭЦП.
Не могу сказать, что на сегодня мы сталкивались с серьезными проблемами при получении каких-либо документов и разрешений, связанных с вопросами экологии. Но впереди получение комплексного экологического разрешения, это большая работа и трудности наверняка возникнут.
— Есть ли вопросы по разработке прогрессивных и эффективных методов переработки и утилизации отходов?
Да, такие вопросы есть. В России довольно трудно получить разрешение на организацию мест хранения отходов, причем не нам, а собственникам полигонов — им приходится проходить очень сложную процедуру. И второй момент — на сегодняшний день в России очень слабо развита система утилизации отходов со строительством специализированных цехов, предприятий, которые занимаются этим системно. Таких предприятий очень мало и в нашем городе Кемерово, но этим вопросом сейчас довольно серьезно занимаются на федеральном уровне.
Нам нужны безотходные технологии, у нас всегда есть запросы на модернизацию очистных систем, разработку технологий, направленных на снижение, минимизацию отходов производства. В этом направлении мы ведем большую работу. Президент поставил задачу к 2024 году снизить выбросы на 20%, мы разработали программу мероприятий для достижения целевого показателя и будем ее выполнять.
Есть отходы, которые нам удается продать, часть мы утилизируем у себя, но большую часть размещаем на полигонах. В настоящее время завод имеет ряд договоров по утилизации отходов, в том числе полиэтилена/полипропилена, макулатуры, отработанных масел, отработанных шин, ртутных ламп и т.д. К этим компаниям претензий нет. Большая проблема – утилизация специфических отходов, так называемых технологических. К сожалению, компаний, специализирующихся на этом виде отходов, на рынке либо немного, либо нет совсем. Это наша головная боль.
— Насколько цифровизация помогает сегодня решению задач промышленной экологии? Каким приборам учета Вы отдаете предпочтение – российским или импортным, и почему?
Цифровизация, конечно, помогает. Раньше мы контролировали выбросы только по результатам лабораторных анализов, которые проводились на регулярной основе, но по определенному графику, а как ведут себя выбросы между заборами данных, не видели и могли только предполагать. С внедрением системы автоматического контроля мы постоянно, в течение 24 часов фиксируем показатели, а когда картина происходящего ясна, ситуацией легче управлять. В 2019-2020 году мы внедрили 4 системы автоматизированного контроля выбросов на основных наших источниках, они измеряют и расход, и состав выбросов. Согласно нашей программе, до 2023 года на всех источниках, попадающих под законодательство, у нас будут установлены такие системы.
Что касается приборов учета, то на сегодняшний день все приборы, которые установлены, являются импортными. Опыт производства таких приборов и их эксплуатации за рубежом более длительный, чем в России, поэтому пока мы отдаем предпочтение импортным изделиям. Мы также внедряем системы расширенного управления технологическим процессом, основанные на построении математических моделей, например, такие системы имеются на печах агрегатов аммиака. Это помогает стабилизировать ведение технологического процесса, снизить влияние человеческого фактора, стабилизировать процесс горения и, как следствие, снизить выбросы. Но и здесь разработчик — зарубежный лицензиар.
Татьяна Чечурова,
начальник отдела по связям с общественностью КАО "Азот",
пресс-служба РСХ
